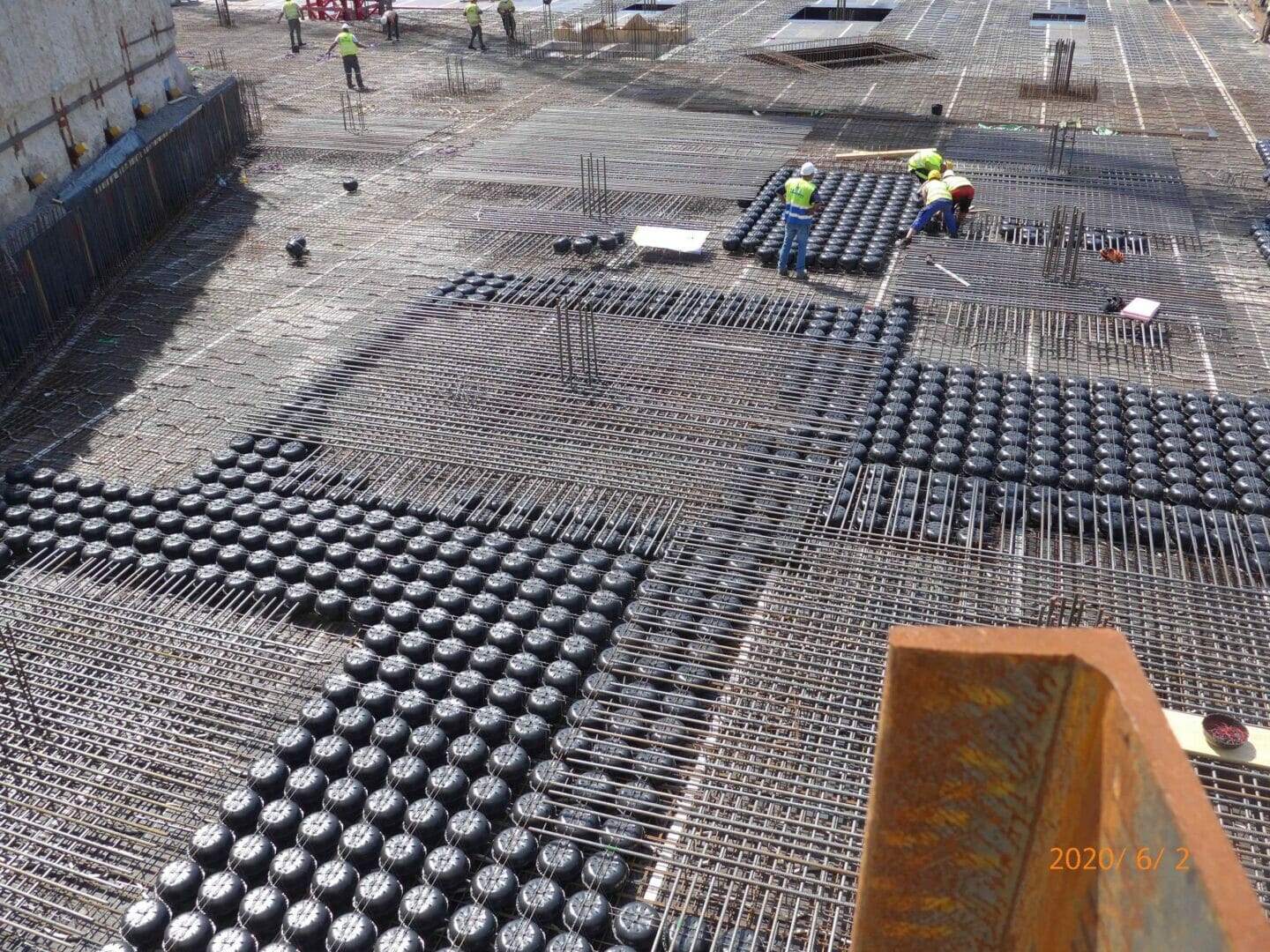
Sustainable technology achieves savings of 286 tonnes of CO2
The Dreiländergalerie in Weil am Rhein is a new shopping and service centre currently being built in a central inner-city location. As well as a tight schedule, a series of construction-related planning changes posed the greatest challenge. One of the buildings was to have an extra floor added, to create more space for retail. Increasing the total weight of the building as a result of this was not an option, as otherwise the earthquake resilience verification would have been compromised, and extensive reinforcement work would have been needed on the walls and foundation slabs. On advice from structural engineers ASSMANN BERATEN + PLANEN GmbH, the building management company CEMAGG Weil am Rhein GmbH & Co. KG decided to use void former modules from Heinze Cobiax Germany GmbH right from the second basement floor, to keep the weight of the extended building constant. This saves 3,365 tonnes. This sustainable technology also means lower concrete use: 227 fewer concrete mixer trips are needed, meaning 286 tonnes lower CO2 emissions. Cobiax is doing their bit towards the concept of green energy building, for which LEED Gold certification is being sought.
In future, passengers on the S8 tram line in Weil am Rhein will be able to enjoy some unique views: in a central location on Europaplatz, a service and retail centre is being built under the project name “Dreiländergalerie”, which will incorporate the building housing the tram’s terminus. The complex, which is being project managed by CEMAGG Weil am Rhein GmbH & Co. KG, comprises a main building and a standalone tower, connected on the upper floor and traversed by the tram at ground level. Upon completion, the building, designed by the Düsseldorf office of Chapman Taylor following plans by architect Yvonne von Salm, will have 26,500 m² of retail space, enough for 550 parking spaces, 60-70 shops and restaurants, and other services besides.
“In addition to the tight schedule, the biggest structural challenges were the geographical location, being in a seismic zone 3, and the subsequent expansion of the building,” claims Christof Hülsmann, structural planner in charge at ASSMANN BERATEN + PLANEN GmbH. “When the client asked about potentially adding an extra floor, the foundations and two lower floors had already been constructed. The extra loading which had to be taken into account with an optional third floor presented a challenge, especially for verifying earthquake resilience.” In the event of earth tremors, the extra weight places greater loading on the strengthening stair cores and their foundations. In conventional design, the option of adding a floor would only have been possible using complex reinforcement structures on the walls and foundation slabs, which had already been manufactured. So the structural engineer recommended using void former modules from Heinze Cobiax Deutschland GmbH, which are made from 100 per cent recycled plastic. They have been installed starting from the second basement floor, to keep the weight of the extended building constant. “Thanks to void former technology, we were able to prepare the building for the potential addition of another floor without disrupting or even interrupting the construction process that had already started,” claims Jana Knoppe, project manager at Drees & Sommer as client representative for CEMAGG.
Using void former technology saves 3,365 tonnes in weight
The building was initially scoped with point-supported reinforced concrete slabs with no void formers. But, by using these starting from the slab above the second basement floor, the dead weight of the floor slabs can now be reduced, significantly reducing the loading on the load-bearing and strengthening building elements. To this end, around 108,000 void formers have been used in precisely predefined, structurally non-critical areas, resulting in a total void former slab area of around 35,000 m2. Due to different slab thicknesses, various versions of the Cobiax SL and EL systems are used (including SL-100-120.7, SL-M-140-160.7 and EL-M-360), some being pre-assembled and others delivered as parts for assembly at the construction site. “The different slab thicknesses arise because there are different span requirements in the underground car park, retail areas, shopping area, covered areas and storerooms,” says Hülsmann. “Due to zone 3 seismic activity, particular design requirements had to be met in accordance with DIN 4149: 2005 in any areas holding up the point-supported slabs, affecting the layout of the void formers.” According to the structural design, structural shear reinforcement needs to be installed around the columns and mushroom piling, so the distances between the void formers and these points are somewhat greater than in buildings with no earthquake resilience verification. There are also variations in the void former heights around the point supports, where larger extra rebar structures are required.
The void formers reduce the expected total weight of the extended building by around 3,365 tonnes. “Using our technology not only means a huge improvement in terms of the weight of the building,” explains Barbara Staab, project manager at Heinze Cobiax Germany. “By reducing the amount of concrete and so too the amount of cement, there is also an environmental benefit that cannot be ignored, as 227 fewer concrete deliveries are now needed. According to our calculations, savings in the case of the Dreiländergalerie amounted to 286 tonnes of CO2.” The noticeable reduction in construction site traffic and the resource-saving construction method fit in very well with the green energy concept behind the shopping and service centre, which includes heating from a CHP unit.
Support during planning and on site
Cobiax in fact provided extensive support during project planning, to ensure the best possible configuration of void formers. For example, existing height differences between two reinforcement layers could be compensated for by using two different void former sizes. “Cobiax has been actively involved in the planning process and has teamed up automatically and smoothly with everyone involved in the construction as needed, such as the structural engineer, reviewer and site management,” confirms Hülsmann. The building complex, which is to be certified in accordance with LEED Gold, is marked for completion at the end of 2021. The Dreiländergalerie will then be handed over for its new life as a service and retail centre. In fact, the complex has already welcomed a distinguished visitor during construction: the German children’s tv programme “Die Sendung mit der Maus” was enthusiastic about the void formers, reporting in one episode on the benefits of this design.
Further information on the website at: green.cobiax.de