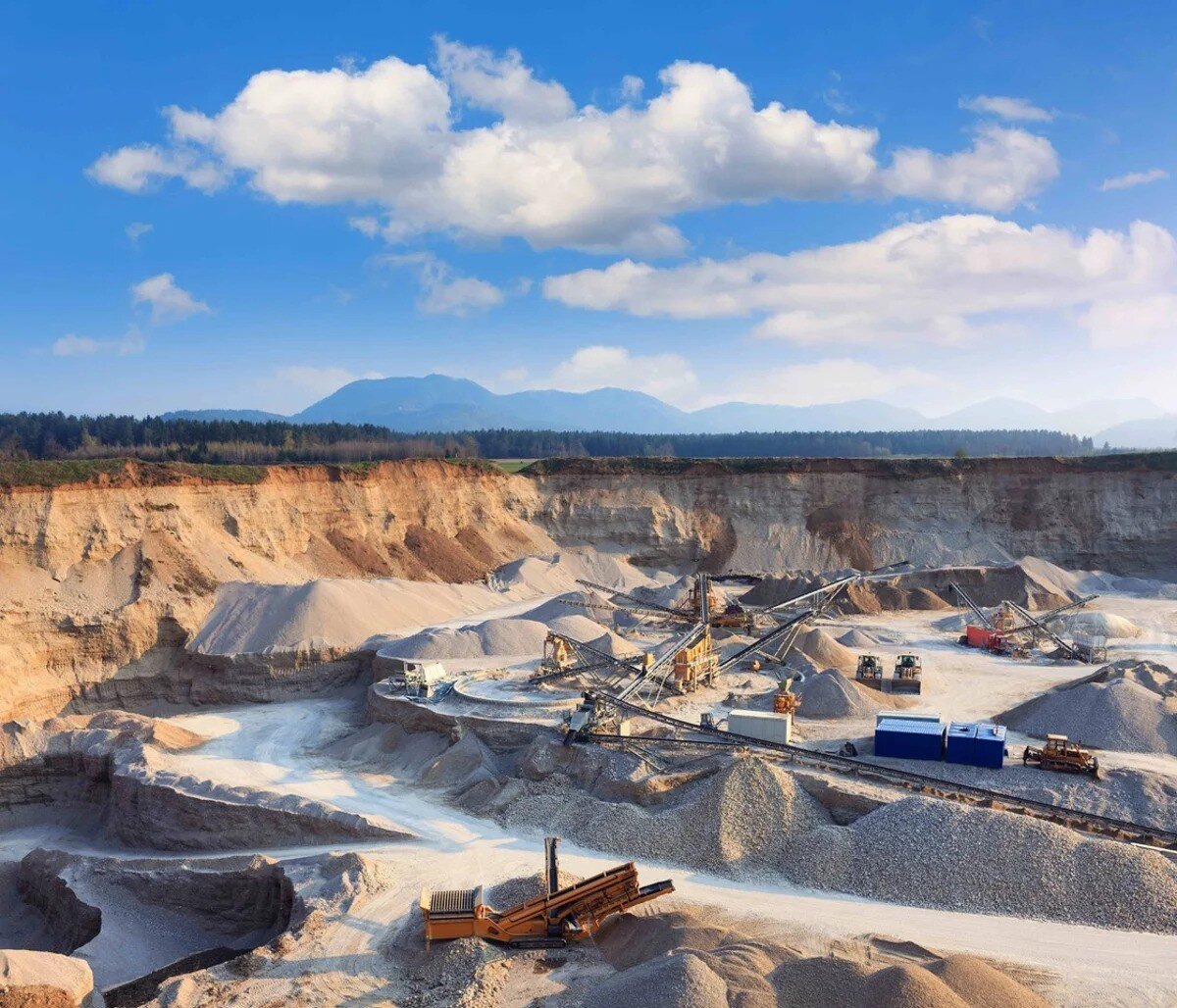
Dellner Group is driving continued improvement of best practices in mining, which is a challenging industry that places unique demands on safety critical components.
Dellner Bubenzer, a manufacturer of high-performance disc and drum brakes, cylinders, and accumulators for mining, cranes, and other severe duty applications, is well positioned to promote the value of components and ancillary equipment to mines — one of the world’s most demanding industries. It is continually raising awareness of the importance of safety critical braking solutions, supported by a global operation, as we’ll explore.
The Dellner brand has been synonymous with industrial braking and safety since Dellner Brakes was founded in 1941, but it has been a story of perpetual motion, right up to and beyond the 2021 acquisition of Dellner Hydratech, the Danish supplier of high-end hydraulic systems, cylinders, and accumulators for mining, wind, offshore, and marine applications. Other historic moments include the acquisition of Pintsch Bubenzer in 2018, leading to the formation of the Dellner Bubenzer Group.
The company has repeatedly delivered solutions to heavy-duty mining projects in recent years. In addition to its main market — material handling — the mining sector presents many challenges that require the company to respond with efficiency and precision, and produce targeted, tailor-made products. This ability sees Dellner Bubenzer stand out not only in material handling and mining, but a myriad of other sectors besides.
A unique market
Mining is different to other markets, most notably because of the lead and project times in play, in addition to the demands placed on equipment at the point of use.
Where a manufacturer of container handling equipment might complete production on a crane every single day, the largest mining companies — BHP Group, Rio Tinto, Glencore Plc, Vale SA, and China Shenhua Energy Co. Ltd., etc. — might be working to a site starting to mine a year from Dellner Bubenzer first being consulted. However, that point in time is non-negotiable and everyone has to deliver — on schedule and on budget.
It is also not uncommon for component manufacturers to have service engineers on site for months at a time, which wouldn’t be the case in the material handling market. And, while a lot of industries work to high duty cycles, mines are expected to be operational 24-hours-a-day, seven-days-a-week.
Mongolia, North of China, is just one of a number of mining hotbeds consuming Dellner Bubenzer’s solutions (see insert). Further demand is being generated by China itself, India, and South America, where a wide variety of raw materials are mined — from rare earths to precious metals. Africa, meanwhile, represents a more embryonic marketplace.
In each case, the requirements are different. One project can be underground, another one at an altitude of 5,000 metres. Then there are projects with above-ground conveyor belts that descend and then rise sharply. Conveyor belts and elevators present a clear and obvious need for braking solutions. Belts must come to a safe standstill in the event of a drive failure, depending on the load and speed. Especially during power outages, the belts must stop in a controlled manner with longer braking times. An immediate stop by directly applying the brakes would lead to destruction of the conveyor belt and, in the worst case, wrecking of everything surrounding it.
The mining sector continues to sharpen its focus on health and safety surrounding conveyor belts and elevators. The controlled stop prevents the belt from being destroyed along with the load but, importantly, this also prevents human injuries if people are near the band.
Contamination prevention High-end hydraulic cylinders and accumulators are central to Dellner Hydratech’s mining portfolio. Hydraulic cylinders generate a pulling or pushing force; they are found, among other places, in earth-moving equipment in surface applications. Steering, bucket, and lift cylinders can be found on a single wheeled loader. Accumulators, meanwhile, are a type of pressure storage hardware where an incompressible hydraulic fluid is held under pressure and applied mechanically. An overarching concern with such technologies — they are required to work in dirty, heavy-duty environments — is contamination. These systems have multiple components and when they become contaminated costly downtime is endured. In fact, over 70% of failed cylinders have broken down due to contamination and Dellner is contacted daily about inferior systems breaking for the same reason. All weld details must be optimised for high fatigue strength and to eliminate the risk of contaminating internal parts of the cylinder. Metal to metal gaps at welds must be avoided, as dirt can be trapped and released when parts expand at high pressure. Dellner recently improved the 800-hour lifetime of a cylinder by five times, ‘simply’ by removing the risk of contamination. |
Global operation, local service
Dellner Bubenzer Germany is part of the company’s industrial business division, and is currently answering all enquiries regarding mining, supported by automation engineers, commissioning teams, and the firm’s research and development department. Sales, technical functions, and commercial calculations all take place at the same facility too, meaning contracts can be handled from start to finish within a single office. Dellner Bubenzer recognises, however, that proximity to the point of use is especially important to after-sales.
Dellner strategically locates its product development and manufacturing facilities across the globe to efficiently serve the mining industry. Presently, Dellner Bubenzer maintains manufacturing / service facilities and operational bases in several key regions, including Europe, Asia, and North America. These global facilities are positioned to ensure proximity to major mining markets, facilitating streamlined production processes and prompt delivery of braking solutions to mining operations, wherever they might be.
Andreas Schneider is technically responsible in Germany for mining, but each of the Asia; Europe / Middle East / Africa (EMEA); and U.S. has its own sales director. An additional sales manager for mining is part of a current recruitment drive, with after-sales support globally a key focus area.
Service, maintenance, and after-sales support are evidently paramount to the mining sector. Downtime due to equipment failure can result in significant financial losses and safety hazards. Component manufacturers must be committed to providing comprehensive maintenance services, timely repairs, and technical assistance to ensure continuous operation. Achieving this requires meticulous maintenance planning and availability of spare parts.
Equally crucial is having trained personnel on-site who cannot only identify issues but also promptly and safely install replacement parts. To meet this requirement, Dellner Bubenzer offers specialised training sessions to continuously sharpen the necessary skills and knowledge for effectively addressing maintenance and repair tasks.
Product of innovation Dellner Bubenzer has a broad portfolio of products suited to mining applications, key to which is its Bubenzer conveyor control (BCC). Its brakes, meanwhile, as well as being at home in the material handling business, are perfect for the environmental conditions found in mining. Continually popular are its SB series brakes; BUEL thrusters; disc brakes (BSC, SF); pneumatic clutches; hydraulic cylinders; offline oil filtration; and belt conveyor control systems. Dellner Bubenzer is renowned for bringing new products to market. Last year, it introduced a new generation of monitoring system, called the IO link, which it calls the future of predictive maintenance. The GREEN BUEL, meanwhile, consumes 60% less electrical power when the brake needs to operate. Product evolution largely centres on creating more opportunities to detect a system fault at an early stage before a failure occurs and systems come to a standstill. The brakes are a safety component in all applications and all components must be permanently available in a fail-safe manner. |
See Dellner Bubenzer in Australia, India, USA, and Peru this year. QME, Australia, 23-25 July Mine Expo International, Las Vegas, 24-26 September Perumin, Peru, 25-29 September Expo Cobre, Peru, 28-31 October IMME, India, 20-23 November |
Mine’s a brake Dellner Bubenzer supplied brakes for three gearless conveyor systems with an installed capacity of 2 x 5,500 kW each for 7100 t/h for a copper mine in Mongolia. The full scope of work included floating calliper brakes (model SFR50), brake discs, hydraulic power units, UPS, BCC3000 closed loop control systems, as well as the complete encoder technology. The main parameters of the brake — pad wear, stroke (air gap), and brake pad temperature — are now continuously monitored. The brakes stop the conveyor within 10 seconds in loaded or unloaded condition. Depending on load, speed, etc., the HPU and control unit provide different braking levels and scenarios. The controlled braking process minimises the conveyor belt tension and reduces stresses in the connected equipment. The system is also able to perform the pre-programmed ramps and stopping curves after a power outage. Redundant controls and HPUs guarantee highest system availability. The environmental conditions need a compact set-up of the brake units. The spring applied, hydraulically released, fail-safe brakes are able to equalise axial movement of the connected shafts. Communication between main PLC and BCC3000 goes via PROFIsafe protocol integrating the relevant safety features while also monitoring the sub-functions. |
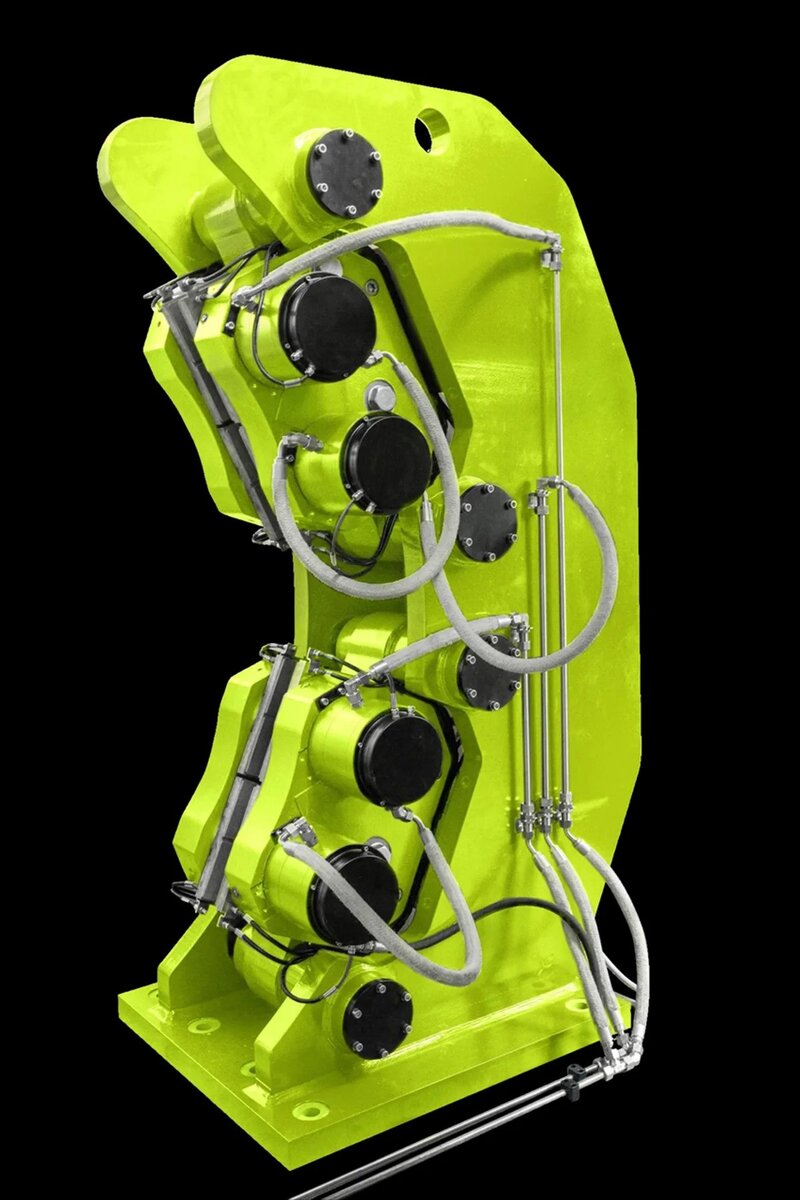
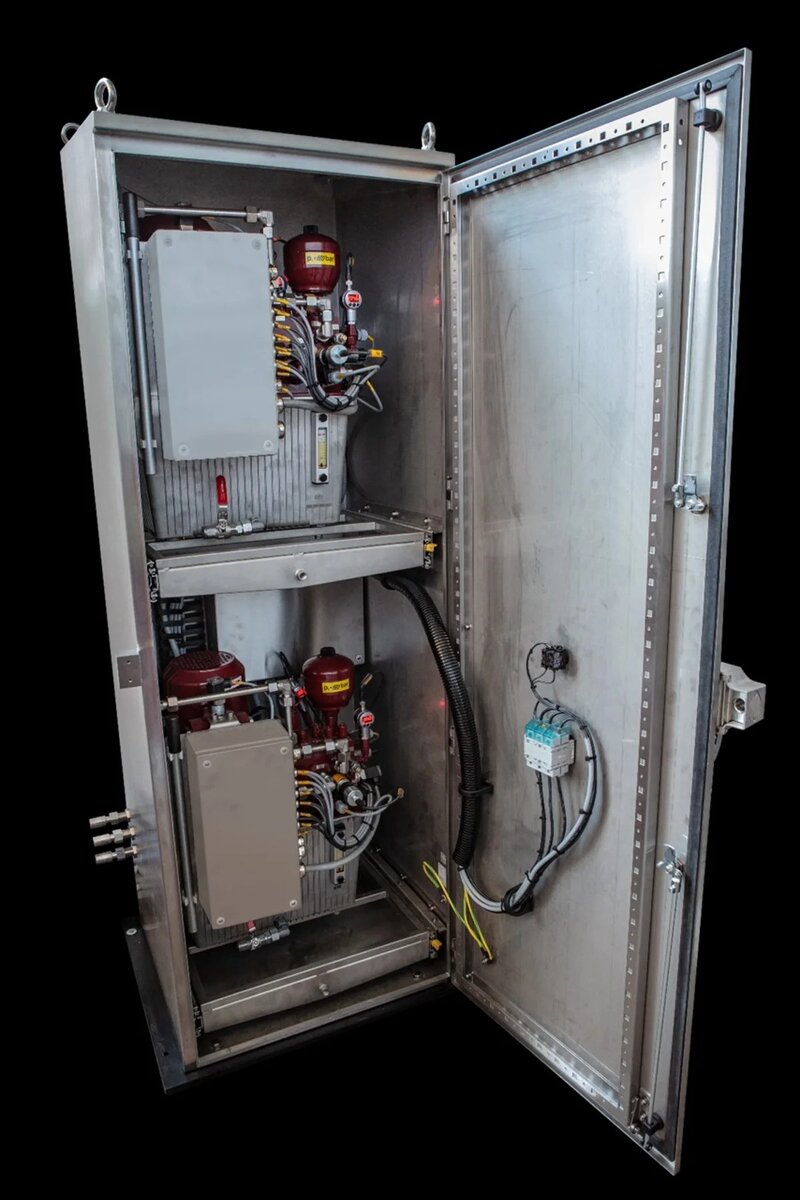