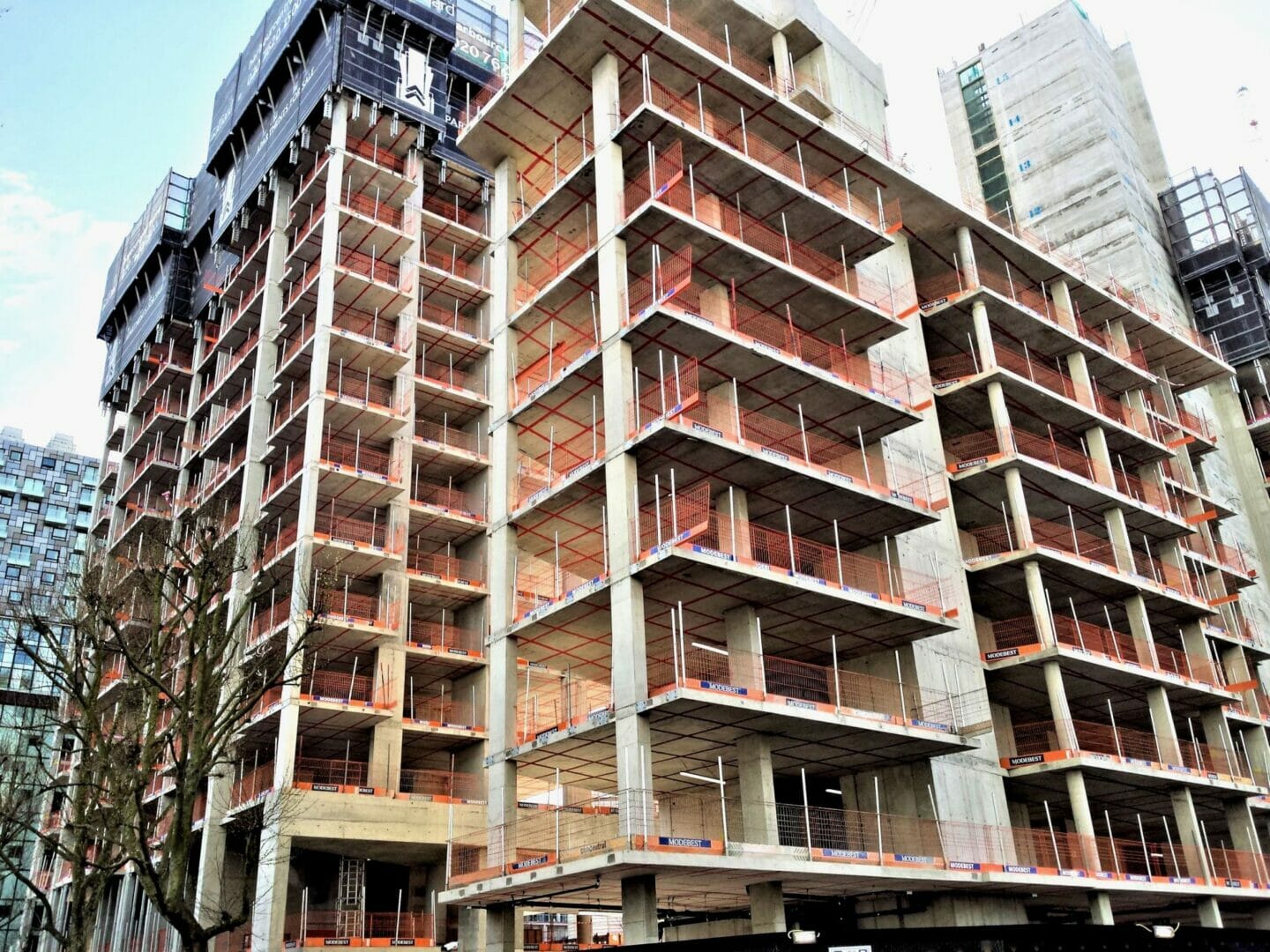
With flat slab construction, there is the inevitable risk of punching failure. So when loads in the stress areas are increased, consideration has to be given to issues such as the quality of the concrete, additional reinforcement content, even enlarging the column heads. These options are neither time efficient nor cost effective, and rarely solve the problem to an acceptable performance level. Resolving any potential problems of punching shear at the major new Harbour Central development needed to be cost-effective, easy-to-install and certainly dependable.
Canary Wharf, in Docklands, is home to some of the UK’s most high profile buildings and the latest addition to the skyline in East London is Harbour Central. Located just a few hundred metres to the south of Canary Wharf, on the far side of South Dock at Millharbour; it is an exciting mixed-use development covering an area of around 1000 hectares. Seven, new buildings, ranging in height from eight to forty-two storeys, will deliver over 900 new homes as a mix of one, two, three and four bed homes, along with eight exceptional penthouse apartments. All of which sit alongside retail and leisure facilities designed around two green squares High-rise glass and bronze clad 35 and 42 storey residential towers dominate the development. The focal point of the development is Maine Tower, a marker building which offers 297 extremely high specification apartments with exceptional views from the upper floors. The tower also features a New York-style lounge, a library, gym, spa and cocktail bar. Historically the site used to be a grain storage area and the design concept of the building picks up on this organic ‘wheat stalk’ theme by breaking it up vertically into eight storey segments, made up of four storey ‘pods’.
Preventing punching failure is critical
Construction at Harbour Central involves a large single-storey reinforced concrete basement, high-rise reinforced concrete cores and frames up to 42 storeys. The high-rise reinforced tower cores utilise a slip-form method of construction and all suspended reinforced concrete slabs are constructed using a post tensioning system. Flat slab floor is of course primarily an economical form of construction, but it offers other benefits as well. The minimisation of shuttering time for example, simplification of reinforcement work, ease of underslab work such as ducting and just as importantly, the optimum use of space. However, with flat slab construction the risk of punching failure is always a critical issue. When increasing the loads in the stress areas, a great deal of consideration has to be given to variables such as the quality of the concrete itself, improving the reinforcement content and even enlarging the column heads. None of these options is necessarily time efficient or cost effective. They rarely solve the problem to an acceptable performance level either. So the ideal solution to resolving any potential problems of punching shear, needs to be cost-effective, easy-to-install and certainly dependable.
Increased shear force resistance of around 70%
The Schöck Bole reinforcement system is used to prevent punching failure throughout the Harbour Central development. This widely used and trusted solution consists of double-headed studs and anchors, with spacing bars, which enable installation after the bottom reinforcement and before the top layer. Two spacer bars are welded to the vertical studs, which ensure the correct distance between uprights; and the forged stud heads guarantee a perfect finishing bond with the concrete. As result, when compared with a typical stirrup reinforcement system, an increased shear force resistance of around 70% is achievable. It is a cost-effective and timesaving solution and as the Modebest Senior Engineer on site, Sean Togher commented: “The Schöck Bole product was easy to understand from a reference point of view and we found it really straightforward to install”.
Other variants – plus Schöck design software too
In addition to the standard Bole solution, Schöck has developed three other punching shear reinforcement variants. The type U is a solution designed for installation before the lower mat; the type O is for installation after the top reinforcement layer; and the type F is designed for use in element slabs at prefabricating plants. The entire range is supplied ready for installation and provides a totally reliable solution to the problem of punching shear in flat slabs. There is downloadable user-friendly Schöck design software available too, which enables fast and simple dimensioning of the product to British Standards and the export of CAD drawings with dxf-format.
For further information on the Schöck Bole system contact the company on 01865 290 890 or visit www.schoeck.co.uk