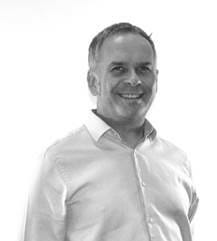
When it comes to designing emergency lighting, there are many factors to consider. Peter Adams, Mackwell’s Central Service & Training Manager explains more.
Not only must the emergency lighting system be fit for purpose, but it must also meet stringent safety and compliance standards. Meeting these standards can impact financially, both in terms of the design and specification, through to the installation, and the on-going maintenance of the system. Often portrayed as a necessary but unattractive part of the lighting scheme, emergency lighting is in fact, a safety critical system and is a legal requirement within commercial premises. It is provided to help facilitate the immediate and safe evacuation of occupants from the premises in times of emergency and as such, must be afforded the same importance and diligence of other such systems. Short cuts and corner cutting such as the specification of sub-standard components and ineffective maintenance schedules, brought about by budgetary constraints can all result in non-compliances, compromising the safety of the building occupants.
One of the most fundamental aspects of building safety, the provision of an adequate emergency lighting system, can often be overlooked. Its importance, however, is critical in ensuring the safety of employees and members of the public. Emergency lighting provides guidance and illumination of a sufficiently high level to enable all occupants to evacuate the premises safely at times of emergency. The consequences of a non-compliant emergency lighting system can impact severely on the health and safety of occupants, resulting in prosecutions such as fines and custodial sentences depending on the level of non-compliance.
British Standards
With the extensive revision of BS 5266 – 1: Code of practice for the emergency lighting of premises (released May 2016 and brought into force in June 2017), the way designers approach emergency lighting has fundamentally changed. Despite better defined responsibilities and more detail on emergency safety lighting and standby lighting requirements, the area is now more complex with greater scope for confusion between parties responsible for the design, installation, testing/commissioning and ongoing performance of the emergency lighting system.
As with most aspects of health and safety, there are many national and international standards in place to ensure that such systems can perform the tasks demanded of them. It is therefore imperative that the constituent components of the emergency lighting system are selected, designed and installed to the specific criteria within these standards, ensuring compliance and performance of both the components and the system as a whole.
The Code of practice, BS 5266 :1999 – 2016, is an essential point of reference. Its accompanying standard; BS 5266 Part 7 – EN 1838: 2013, defines the minimum lux levels and photometric requirements when designing the emergency lighting scheme. Also, in place is the standard; BS EN 60598-2-22: 2014, for luminaires used in emergency lighting and ensures that they achieve the performance required whilst remaining electrically and mechanically safe.
In addition, the European Application Standard with improved testing regimes, EN 50172: 2004, is a vital supporting part of the BS 5266 series.
The design objective for any emergency lighting system is established by BS 5266 Section 5.2.1 which says that, when the supply to the normal lighting fails, emergency lighting is required to:
- indicate clearly the escape routes
- provide illumination along such routes to allow safe movement through the exits
- ensure that fire-alarm and fire-fighting equipment can be readily located
British and European Standards provide guidance on the implementation of requirements and solutions, on sustainability and energy use, guidance on required equipment, lighting for specific specialist areas as well as guidance on the installation process, testing and commissioning – all of which need to be considered at the start of the design process.
It is also important for the manufacturer to understand the intended environment for the luminaire in order to specify the correct safety components. Although there is currently no legislation covering the use of LS ZH (low smoke, zero halogen) components, it is recommended that LSZH be used in fittings specified for use in large public areas where there is a risk of fire. This will minimize the risk from the after effects of an electrical fire, such as gas and smoke inhalation. For example, after the Kings Cross fire in 1987, LSZH sheathing became mandatory for all electrical wiring in London Underground Stations.
Compliance
In order for the emergency lighting system to remain compliant throughout its lifetime, structured and effective maintenance is essential. The system requires testing in line with the requirements specified in BS EN 50172, together with any remedial action which is identified by these tests. Routine visual inspection of the system is also fundamental to check for any changes to décor, colour schemes, fabric and structure together with any reparations which may impact the designed scheme. Unlike a fire alarm system which is generally subjected to a simple, periodic audible test for functionality, (albeit in line with an annual sub-contracted service contract), the maintenance of the emergency lighting system is more time consuming if being undertaken manually, without the aid of an automatic test facility, The annual full discharge test of up to three hours duration may need to be staggered across different storeys and areas within the building and this may be perceived as a costly and labour intensive overhead. What value can be put on the health and safety of occupants though? The effect of the emergency lighting is seldom seen until required, and it is during these times, where the safe and immediate evacuation of the building is paramount, that we come to appreciate the true value of this safety critical system.
Luminaires
The cumulative operating costs of emergency lighting can be considerable, and the choice of fitting should be considered in terms of its installation cost, long-term energy consumption and maintenance or replacement costs. LED’s consume about 25% of the power of traditional lamps and offer excellent lumen maintenance as the light output remains constant throughout its design life. The greatest cost benefit, however, relates to lamp replacement. LED lamps typically have a 50,000h rated life, ten times that of a typical fluorescent tube. Using LED emergency luminaires will greatly reduce the maintenance costs of an emergency lighting system and they have a longer expected life and lower running costs than standard luminaires.
Batteries
Batteries also have an impact on the cost of luminaires intended for emergency lighting, with Nickel-cadmium (NiCd) batteries the preferred choice for self-contained luminaires despite the fact that they utilise a toxic metal. However, Nickel-Metal Hydride (NiMH) batteries offer a viable alternative with significant benefits over the Nickel-cadmium battery. The NiMH battery offers an energy density two to three times that of the NiCd battery, meaning it can be a third of the size of the NiCd equivalent. Combined with a LED light source and appropriate charger, this can result in a very compact package. Another significant benefit is the charging regime. NiCd batteries require a constant current charge, NiMH batteries however, have an excellent rapid-charge capability meaning they can be given a boost charge followed by a trickle charge. This results in long term energy savings, reducing ongoing costs.
Testing
Statistical evidence indicates that regular testing and maintenance of emergency lighting systems is not routinely carried out by many organisations as it is laborious and time consuming, and therefore expensive. However, the fines for non-compliance are more so and eventually puts lives at risk.
Testing of the emergency lighting system should be carried out at regular intervals by a qualified person. The tests must be carried out in line with the schedules outlined in BS EN 50172 as below:
- Daily – visual check that all charge indicators are lit on and check lamps on all maintained luminaires are working.
- Monthly – a monthly functional test is designed to simulate a failure of normal lighting for sufficient time to allow all emergency luminaires to be checked for correct operation and signs of damage or deterioration and the results recorded in a log book.
- Annually – a test simulating the failure of the normal lighting supply for the full emergency duration (typically 3 hours) to ensure that the emergency luminaires can function for the full duration whilst maintaining their declared emergency output or ballast lumen factor figures. During this test, the batteries will be discharged, and the luminaires will not be fully operational until they have had time to recharge. Therefore, this test is normally carried out whilst the building is unoccupied and at periods of low risk.
Maintenance
Traditionally industry practice has been to replace the whole emergency fitting if it fails the annual test as it was believed that this was more economical than isolating the circuit to replace the faulty component, usually the battery. This often results in emergency fittings being replaced every 3 to 4 years, but by choosing a fitting that allows for easy removal for repair and upgrade and an accessible battery drawer, the life span of the unit can be considerably increased, reducing long-term maintenance and replacement costs.
Keeping emergency lighting luminaires clean is vital to lighting efficiency. Over time dirt, grease and the build-up of insects inside the light fitting can reduce the light levels and can reduce the illumination by up to 30%, potentially falling below minimum lighting levels. This could mean a test failure and result in a non-compliance.
Monitoring Solutions
There are systems available which will make the testing process easier and less expensive, the upfront costs are similar to installing a standard emergency lighting system, but the payback is the long-term maintenance and testing cost savings.
- Self-test Emergency luminaires provide simple ‘stand-alone’ automatic testing and the result of the test is indicated through a bi-colour LED on the luminaire. Monthly checks will still need to be carried out by the responsible person and the test results recorded and entered into the log book. However, the benefit of this type of system is that the person recording the information is not required to be qualified as they will not be testing the system manually.
- Automatic Test Systems connect the emergency luminaires to a remote-control panel that collects the results centrally. These systems provide 24/7 monitoring, self-testing and reporting, including remote access to the status of every fitting, automatic record keeping and fault notification. These systems use a low voltage communication signal via an interface such as DALI and can be easily retro-fitted, providing regulatory compliance with minimal effort.
Specification
Compromising on the specification of a fitting at installation can lead to long term maintenance issues, impacting on health and safety. It is a requirement that luminaires chosen for self-contained emergency lighting include a local indicator which is visible in normal operation. These indicators are a valuable aid to maintenance in the first instance, as they provide an immediate indication of the health of the emergency luminaire and that the battery is being charged. If the indicator is green, the luminaire is healthy. They do not, however, negate the requirement for regular safety checks. Emergency lighting systems should be maintained on a regular basis to ensure they are fully functional, the batteries are fully charged and that their light sources remain operational. These checks should be carried out by a suitably qualified responsible person as determined in the fire safety order and the fire safety log book should be updated subsequently to each test. This will ensure that all fire safety legislation is adhered to and that the emergency lighting system remains fully operational, meeting fire safety requirements.
Legal Imperative
Since the introduction of the Fire Regulation Reform Order in 2005, the legal imperative for installing emergency lighting systems is the same as for the fire-alarm systems. Failure to comply with the correct installation of emergency lighting and to maintain the system could cost a business dearly. If fire authorities discover that the emergency lighting system is not fit for purpose or non-compliant, and that the system has not been properly maintained, the company could receive a hefty fine, often in the tens of thousands of pounds. If neglect is proven in terms of the standard of the installation or maintenance of emergency lighting, and leads to injury or worse, the ‘responsible person’ could face a custodial sentence.
The law is drafted to place ultimate responsibility squarely with the owner of the property, but it also names in the act a “responsible person”, who the owner of the property can appoint and delegate that responsibility to. That person is then required to make the necessary provision for emergency lighting, including undertaking risk assessments and having a proper fire safety schedule mapped out. Even if the owner delegates the responsibility, they are still responsible for ensuring that the “responsible person” has been properly trained.
The Regulatory Reform (Fire Safety) Order 2005 requires the installation of emergency and safety lighting and Article 12 of the regulation stipulates that: “Emergency routes and exits must be indicated by signs, and emergency routes and exits requiring illumination, must be provided with emergency lighting of adequate intensity in the case of failure of their normal lighting.” Any breaches of the Order are likely to result in the person responsible facing fines or imprisonment.
For too long, emergency lighting has been viewed as the poorer cousin to the main lighting scheme. Necessary as a legal requirement but ultimately detracting from the general ambience, and interfering with the aesthetics of the design whilst incurring extra expense.
It needn’t be like this, however. In an era of discrete LED light sources together with slim-line control gear fixtures, architectural designs, and effective spacing tables, the emergency lighting luminaires, if used sympathetically, often end up complimenting the designed scheme whilst bringing comfort and reassurance to building operators. To compromise the emergency lighting is to compromise the health and safety at work act, the Fire Safety Order and ultimately, the individual.
Yes, there is a financial impact, but what price can be attached to a human life? Unless we change our attitude to this safety critical system, and give it the respect that it deserves, all too familiar, tragic events associated with non-compliant commercial premises will continue to occur.
As a world leader in the design and manufacture of reliable, innovative electrical components, Mackwell’s emergency lighting products offer some of the best in quality and performance on the market today. Offering an unsurpassed breadth of products such as high-performance luminaires, super-discrete integrated emergency products and architectural exit signs. Emergency lighting is a legal obligation that should never be compromised – safety by choice, not by chance.
Further information is available from Mackwell on 01922 742145 by email [email protected] or by visiting the company’s website at www.mackwell.com