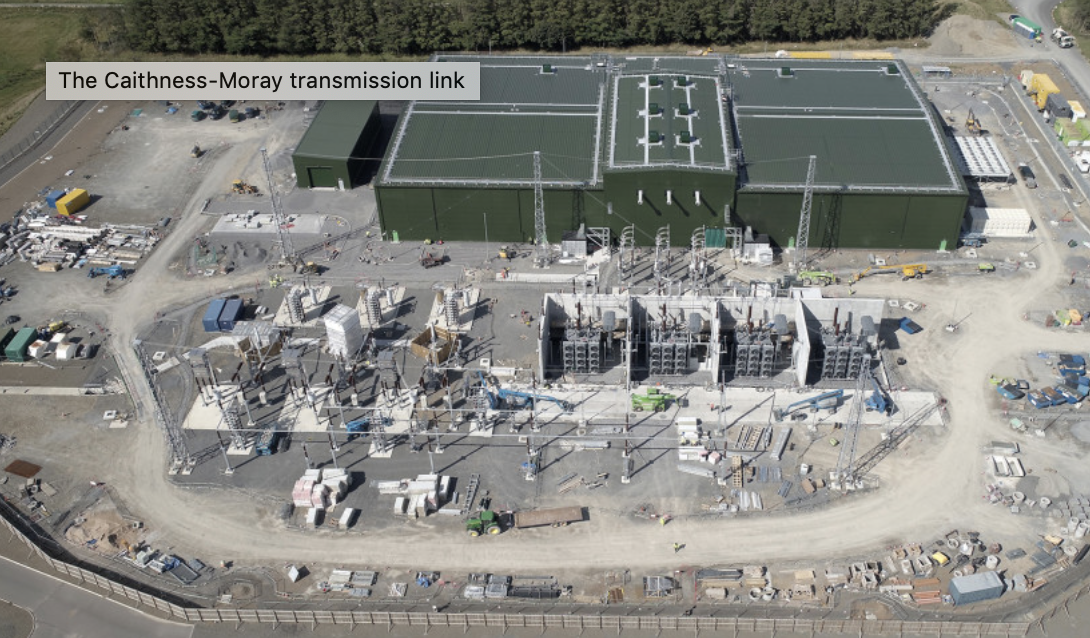
The biggest ever single investment undertaken by SSEN Transmission is now transmitting renewable energy from the north of Scotland.
The company’s Caithness-Moray HVDC transmission link, with a project value of around £1bn, is using the rooftop ventilation system from Gilberts Blackpool to help maintain optimal air flows at the two converter stations at Blackhilock , Moray and Spittal, Caithness.
Caithness-Moray uses HVDC (High Voltage Direct Current) technology to transmit power through a 113km subsea cable beneath the Moray Firth seabed between Spittal and Blackhillock. The two converter stations house 6 supergrid transformers – the largest of their kind in the UK weighing up to 250 tonnes each. The HVDC converter stations process power from on and off-shore wind farms to serve the entire north east of Scotland and beyond.
Gilberts designed and manufactured the 10 rooftop ventilation terminals for the converter stations entirely in-house. Each 1.3m2 with a 1m shaft opening, the penthouses ensure an adequate flow of air into the main DC halls at both locations. A double layer of external louvres with motorised dampers has been engineered to enable appropriate airflow whilst preventing weather ingress at very exposed, aggressive environments.
SSE Enterprise was involved with the installation of the mechanical, electrical and plumbing services on the Caithness-Moray project and their project manager, Thomas McIntosh, said, “It goes without saying that, through the very nature of the converter stations, it is crucial internal temperatures and atmospheres are kept within specific design parameters. As part of the M&E installation, we worked closely with Gilberts and the design team to ensure the right product for what was a challenging job, but one with which we are proud to be involved.”
Said Gilberts’ Technical Director Roy Jones. “The penthouses are among the largest we have ever made and had to be precisely designed and engineered to accommodate the performance levels required. However, as we, uniquely, are entirely self-sufficient in terms of research, design, manufacture and testing, we could confidently work with the contracting team knowing whatever we promised could be delivered.”
Founded 55 years ago, Gilberts Blackpool is unique in its ability to develop components- whether ‘mainstream’ or bespoke – entirely in-house, from initial design through tooling, production, testing and supply, at its 90,000 ft2 manufacturing facility. Its state of the art test centre, designed and built in-house, is one of the most technically advanced in the country.
For further information:
Angela May
AFPR
Tilley Farm Barn, Tilley, Shrops SY4 5HE
Tel/fax: 01939232510; e: [email protected]
Contact information for publication:
Gilberts tel 01253 766911