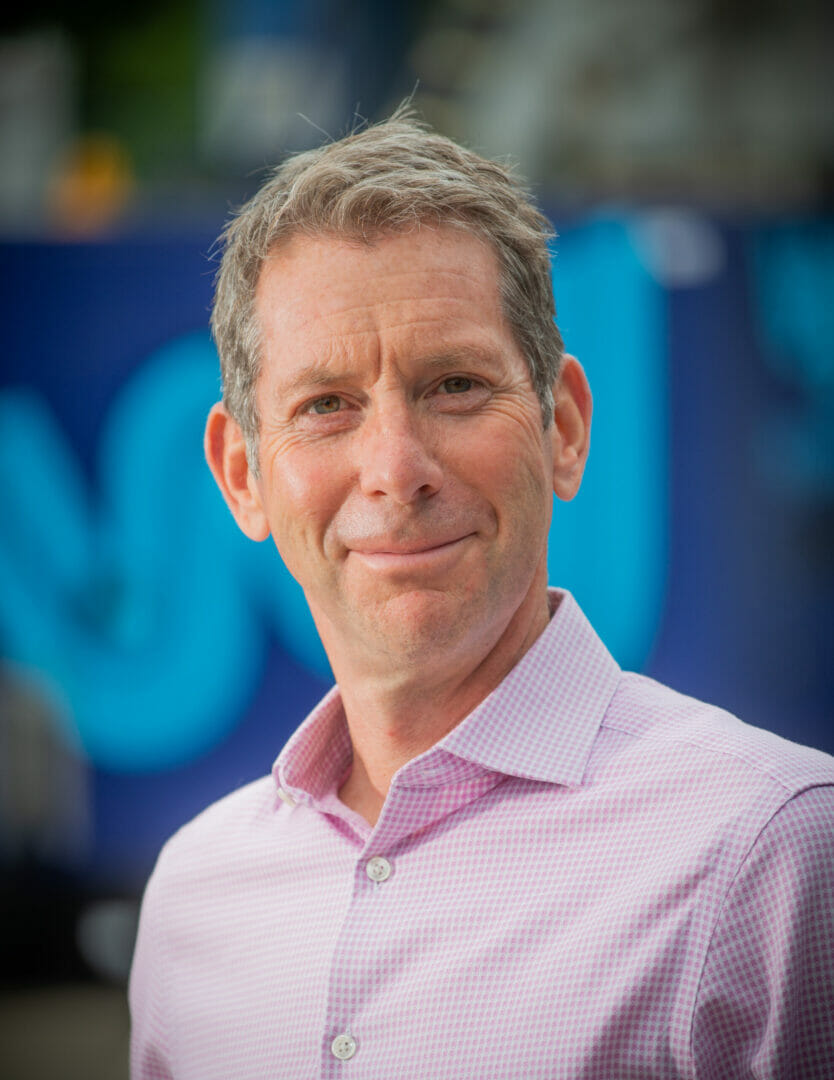
Few would argue that the last few months have been a test for individuals, businesses, and the entire construction sector. COVID-19 has impacted almost every aspect of our lives, and as the short, sharp, shock of it all eases, with the UK slowly returning to some semblance of normality, despite the challenges ahead there are signs of optimism.
Perhaps the most significant is the Government’s continued commitment – reliance maybe – to build our way economically back to good health, which it has backed with the promise of a whole raft of infrastructure projects and finance to support them. All good news then, but this in itself will bring challenges; the main being the high demand these projects will place on the geotechnical disciplines.
The drilling sector was in pretty good shape work-wise pre-COVID-19, although you could argue it was ‘stretched’, with little spare capacity. If public and private sector work appears as it is threatening, then as an industry we must adapt our business models to maximise return on the opportunities as they present themselves. So, what can the already stretched industry be doing to prepare itself for growing demand?
Successful businesses are the result of good workers, dedication, and perseverance, but these alone will only help you tread water. What is needed is innovation – fresh ideas and working methodologies – to keep the customer interested and your operation differentiated to secure new and growing work. It is not just about capacity either, yes bigger means more work can be undertaken, but it is also a competitive environment out there, which means you also have to innovative to stay competitive, and size doesn’t necessarily equal success.
A wide-reaching and cross industry survey conducted by Deloitte back in 2015 showed that 66 percent of companies believed innovation was essential for growth and that businesses that innovate were best able to scale up their structure much more. Quite simply, adding more employees is good, but innovation, investment and continued development helps businesses win more customers, but more importantly, it also makes it easier to grow whatever may be the size and type of your business and meet that growing demand.
What does all this ‘business speak’ mean to the drilling sector? Quite simply it too needs to innovate to succeed, and I like to think it is. One of the most obvious innovations is the development of new, more efficient systems for data acquisition. Systems such as Keynetix’s cloud solution and SOCOTEC’s Packer test kit, for example, are both already in place and Soil Engineering Digital Grouting Records is coming shortly, and all are improving efficiency.
Many companies are investing in new equipment; In fact, a number of British Drilling Association (BDA) members have reported buying new rigs and supporting plant, which considering these purchases have been made recently, is proof of their confidence in the future growth of the sector. Plant innovation is abundant too, such as Strata Geotechnics’ VEMOG RRV Drilling rig, which was engineered specifically to deliver ground investigation work on rail and motorway projects under possession or traffic management. Its customers were needing high quality and ‘to a sufficient depth’ ground investigation to ensure follow on piling works had adequate information and design to ensure there were no delays on site during main works. Developing the VEMOG gives its customers the ability to manage and plan their works without delay and manage the significant risks in the ground. WJ UK has moved plant innovation along too; having recently taken delivery of a Comacchio MC6, it is believed to be the first electric powered, multi-functional geotechnical rig designed to surpass the compliance Standards on diesel emissions from construction plant within city centre low emission zones. Powered by a 75 KW motor the rig is set up for ‘plug and play’ in restricted access sites such as basements, shafts and tunnels where the elimination of diesel exhaust gases and particulates not only protects operatives and site workers from harm, but also benefits wider society. The rig was built to WJ’s own specification, including their own designed and built hydraulic interlocked guard and has already been deployed successfully probe drilling for Thames Tideway.
The importance of innovation is recognised by the BDA in its annual awards, which attracts submissions representing its wide and diverse membership. For example, Atkins Ground Engineering Glasgow showcased an innovative digital data collection tool designed to handle large volumes of data on site efficiently, whilst SOCOTEC profiled its Transducer Packer Slave Realer (TPSR), a transducer packer system that can be lowered up to 100m into a borehole with a wireline winch using an umbilical line to follow the packer assembly. The TPSR transfers water under pressure into the designated test section while digitally recording and monitoring both flow and pressure allowing confirmation of the integrity of the seal formed by packers.
WJ UK used the BDA awards to highlight how working with Ferrovial Agroman Laing O’Rourke JV and their designers AECOM, a groundwater control strategy was developed for the shafts and associated adits and connection tunnels on the Thames Tideway Tunnel. Aarsleff Ground Engineering submitted its solution to reducing road/ travel risk, its carbon footprint and journey times using Google Earth application. Specifically, Google Earth was used to aid estimators in their project proposals, allowing staff to visit project sites, observe site access points to determine appropriate rig type, and see the surrounding environment without having to step foot on site. BAM Ritchies showed how its new application of machine control provided major safety, quality, and programme benefits to its Hinckley Point C nuclear power station project, which required 10,000 ground nails installed to support rock slopes of up to 30m.
Concept Engineering Consultant’s, teaming up with ALS Environmental, entered its End-to-End Digital Sample Management System; covering sample labelling, transportation, storage, testing, reporting and disposal, which it had developed – a paperless system whereby all its sample data is managed and tracked digitally and in full compliance with UKAS ad ISO Accreditations.
But it’s not just about kit mand back-office solutions, people too are critical to the innovation mix, and many BDA members have reported taking on new staff, but more significantly are investing in people; providing training for existing staff in higher level skills, supporting universities, such as SOCOTEC’s sponsoring student places at Southampton University, SEGL providing staff to teach at Leeds University, and Leeds’ students taking placements with BDA members too.
The BDA is committed to developing drillers, and initiatives, such as its Level 3 NVQ, have formalised the upskilling in drilling, as well as delivering better recognition of Drillers and Supervisors, which is essential if the sector is to encourage new entrants into the workforce.
The BDA’s strategy has long been to support the innovation, investment, and development of its members through the provision of the many initiatives it provides, some of which mentioned in this article, and the sector is stronger as a result. Going forward, not just the drilling sector, but the wider construction industry, must continue to innovate and invest inwardly on its processes, procedures and people and then together we will all be safer in our work, happier in what we do and from a business perspective more successful.
Author – Richard Fielden, Chair, British Drilling Association