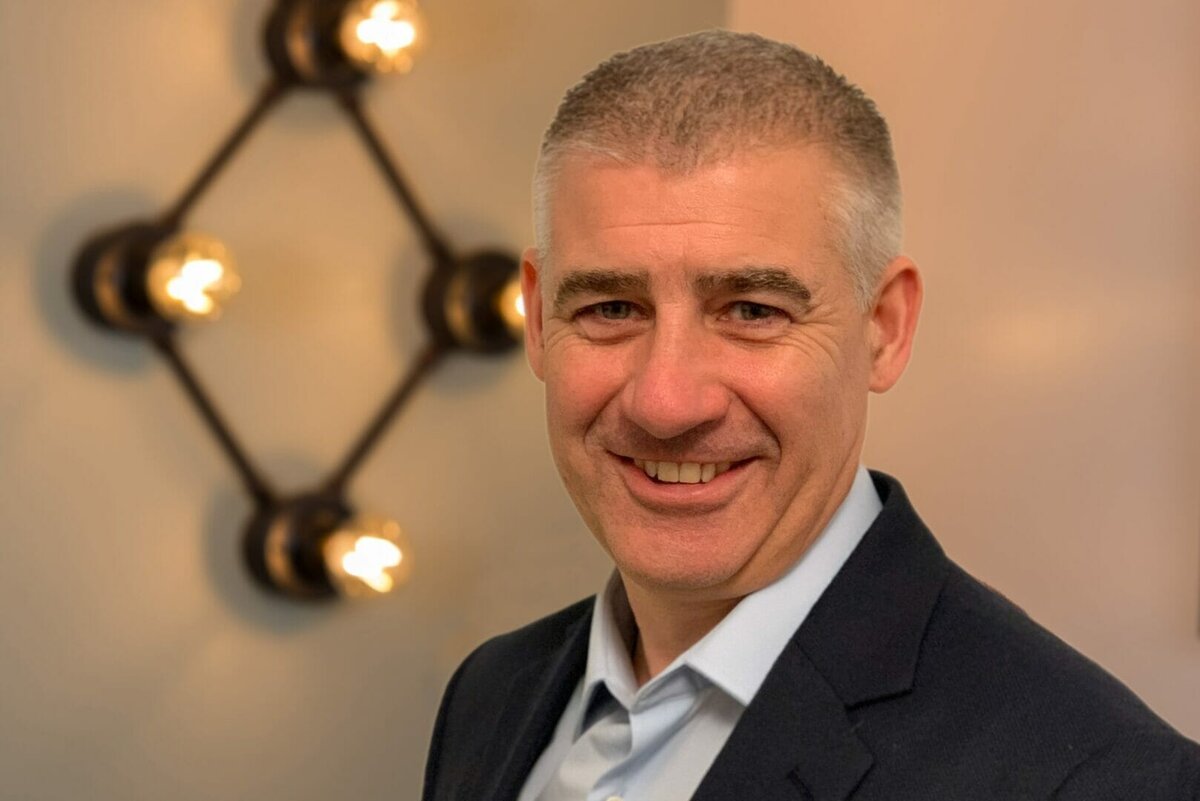
One of the UK’s leading construction experts has called for drastic change in production methods to drive forward the fast-emerging offsite housebuilding industry.
Develop Consulting, the lead transformation consultant, which has over two decades of experience within the field, has warned that current methods, which see modular homes being pre-built in factories using construction methods before being fully assembled on site, needed to be “drastically updated” to achieve success.
Steve Clark, Manufacturing and Construction Director for Develop Consulting, added that for Modern Methods of Construction (MMCs) to truly accelerate the delivery of homes built within the UK, more method change from within was needed within the trade.
He stressed the change from using manufacturing methods rather than those used for construction would not only speed up the build process, but also make it easier, better and cheaper than ever before for new factory-built homes.
Speaking after the recent announcement by chancellor Rishi Sunak that a taskforce was being formed and there would be a £10m injection into the economy to drive the adoption of offsite housebuilding, Mr Clark warned that more needed to be done than just ‘pumping money’ into an industry which needed change at its very core.
Mr Clark said: “There have been millions of pounds spent on the MMC sector over the past five years, with various bodies put together in changing systems and cataloguing parts. But very little has been invested in actually changing behaviours from within.
“The main issue is where the housing is being built offsite, it is done so within a construction culture rather than with a manufacturing process at its core. The manufacturing process within a factory has more planning, organisation and preparation than in any other sector, which gives a far more consistent and streamlined output than anything construction can currently offer. We almost need to create a car assembly line model within a factory setting, but for houses.
“Quite literally we need to build strong foundations for the process of the build to create a stable market, stronger product and this will then lead to an improved output. But the main issue is they aren’t changing the manufacturing facilities into production facilities, they are doing construction under a tin roof, and this needs to change, and soon,” he added.
Mr Clark said Develop Consulting was already working with a number of modular home builders based within the UK to create this change, and urged more to look at transforming this process.
“I honestly believe with this process in place, a company could go from producing one module a day to three, and this would go quite a way to help solving the housing crisis we currently have,” he added.
For more information on the change in process, and for a background on MMCs, click on this link or visit www.develop-consulting.co.uk