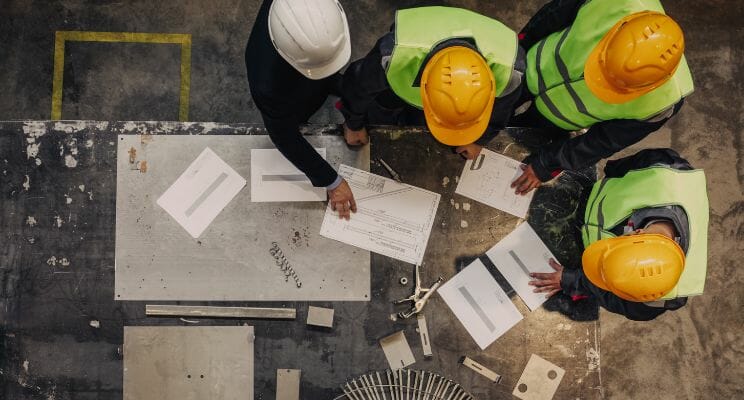
We’re delighted to welcome Terry Box to the Eden Facades team as SHEQ Manager, with responsibility to advise on Safety, Health, Environmental and Quality issues.
With years of health and safety experience, Terry serves as Vice Chair of IOSH Essex Branch committee as well as attending the IOSH Midlands and East Regions Chairs committee and the IOSH Global Chairs committee.
The depth of Terry’s industry knowledge, together with his on-the-job experience, will benefit our clients when it comes to assessing risks on site. We spoke to Terry about his experience, the types of accidents that can occur on site, and some of the steps that can be put in place to reduce risk.
What impact has Covid-19 had on the way Health and Safety is approached and managed on site?
The pandemic has really raised the profile of health and safety professionals; of course, everybody has the intention of keeping their employees safe, but how we go about doing that has really taken centre stage over the last eighteen months or so. The pace was accelerated by COVID and that willingness to adopt new methods of working specifically to protect people has been great to see.
As an industry, we’ve adapted to new ways of working on and off site, such as implementing social distancing, the increased use of digital platforms rather than face to face meetings, and improved cleanliness and hygiene protocols. Sites have been reorganised to accommodate one-way systems, alternative break times and staggered start times to help keep staff safe and projects moving.
What are some of the most common types of accidents that can occur on site?
If safety on a construction site isn’t treated with the seriousness it deserves, accidents are likely to happen. Slips, trips, and falls due to slippery floors or obstructions on site could result in serious physical injuries being sustained, such as broken bones, torn ligaments, or head trauma. Exposure to excessive vibration can lead to permanent injury of the hands and arms, and prolonged exposure to noise can result in temporary or permanent hearing loss.
In addition, construction sites very often contain hazardous substances such as dust, chemicals and fumes that can be harmful, and in some instances cause significant damage to workers’ health.
What are some of the barriers you come across when promoting good health and safety practice on site?
The time pressures and tight deadlines that construction projects are often working to can result in conflicting demands – the need to speed up the process, compared with the need to do it safely.
In my experience with the IOSH, there is sometimes a perception that putting safety procedures in place will be costly, or complicated and time consuming, which can lead to cutting corners. Genuine human error is the greatest challenge to executing proper health and safety procedures on site; more than 85% of accidents, sometimes with serious consequences, are due to poor judgement or a lack of supervision or training.
What are the potential penalties for not having adequate health and safety procedures in place?
The construction industry is one of the UK’s biggest employers, but also one of the most hazardous if safety procedures are not followed. The biggest penalty for not following the correct protocol can be the cost of a human life, or serious illness or injury.
To put emphasis on the importance of protection, there is the potential of a financial cost – legal costs, fines increased insurance premiums cost of replacement staff, time spent on putting things right – as well as the reputational damage which can have impacts of cost as well as recruitment issues.
As an industry, what steps can we take to improving the overall safety of projects?
Health and safety should be the number one priority, no matter what. Health and safety at work is everyone’s concern and we should be working towards a ‘no blame’ culture, where we all look out for each other – not just in our day-to-day activities, but long term.
The expression ‘we shout safety but whisper health’ is more relevant than ever. As health and wellbeing moves higher up the agenda, as an industry we are beginning to recognise the need for a better balance between the two and put more emphasis on health. IOSH’s recently launched ‘Catch the Wave’ campaign calls on businesses to harness the wave of social change by putting the needs and welfare of people first, recognising that businesses with stronger sustainability practices are seeing better performance and growth.
Through setting safety standards such as regular inspections and monitoring right from the beginning of a project, as well as engaging and empowering the workforce through open dialogue and feedback, significant improvements can be made.
How do you work with the Eden Facades team to mitigate health and risk on projects?
As in-house health and safety adviser, I visit sites and can make assessments and recommendations before work starts on a project. I work with the team to prepare RAMS for all projects, in addition to bi-weekly health and safety reports.
Our teams have ‘Toolbox talks’ briefings at the start of every project and all are trained to NVQ level 3 or NVQ level 6. As a company we understand the importance of ‘continuous improvement’, and we are working to achieve International ISO accreditations 9001, 45001 and 14001 alongside our current certifications.
To find out more about how we mitigate health and safety risks on our projects, get in touch on 01268 744199 or email office@edenfacades.co.uk. You can connect with Terry on LinkedIn or follow our company page.