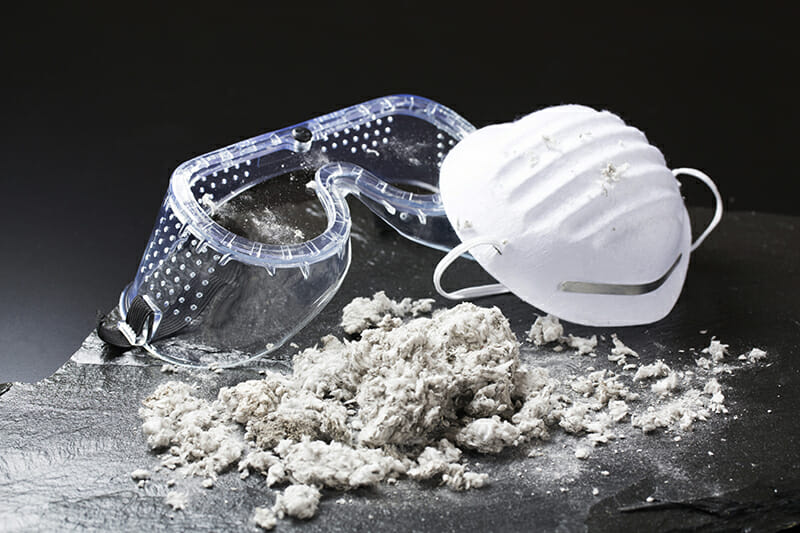
Tim Turney, Global Marketing Manager at occupational hygiene and workplace hazard monitoring expert Casella, shares best practice advice on asbestos monitoring
Asbestos-related diseases take the lives of 20 tradespeople every week.1 Left alone, the material is not harmful, but once disturbed or disintegrating, it can release asbestos fibres that infiltrate and progressively damage the lungs. The damage results in multiple health defects, such as the lung disease mesothelioma — a cancer that can take up to 20 years to develop, proving fatal within five years or less.
Despite being banned in the UK, asbestos can still be found in older homes and industrial properties built between the 1950s and 70s, posing a threat to anyone who disturbs the dangerous material.
Global Asbestos Awareness Week (GAAW) aims to raise awareness of the dangers of asbestos, bringing experts and those affected together to share, learn and act. Understanding how to maximise asbestos monitoring accuracy and minimise risks can help to save lives.
Training and licencing requirements must be met
Discrepancies in sampling and analysis procedures, limitations in personal protective clothing and insufficient cleaning before a clearance pass can hinder accuracy and increase risks. Whenever asbestos is removed, it is a legal requirement to use licenced contractors and to ensure that strict regulations and guidance are followed to limit the potential release of dangerous, airborne fibres. The guidance typically includes personal air sampling and/or static air sampling, to ensure that there is no exposure during remediation work or during the cleaning and clearance processes at a removal site.
In the UK, a four-stage clearance process is used, involving a preliminary check of the site condition and job completeness, a thorough visual inspection inside the enclosure or work area, air monitoring and a final assessment of the post-enclosure or work area following dismantling. Licenced contractors may also take air samples before work is undertaken to establish a background level measurement. Conducting a test before disturbing any materials could save thousands of pounds on decontamination and environmental cleaning fees and help to avoid exposure. Additionally, trained professionals may take air samples during work on or near asbestos to confirm that there is no leakage from the enclosure.
Equipment must be selected, used and maintained correctly
Air sampling pumps should be used for at least one hour after ensuring that equipment meets the relevant standard(s) and has the required flow-range capability, for example, at 12 L/min the required 480L sample can be completed in 40 minutes. Modern pumps can do timed or volume-based runs to achieve better result accuracy. However, reading the manufacturer’s handbook thoroughly before using the equipment can ensure correct use and allow for optimal feature use.
Ensuring air sampling equipment has an accurate flow rate to ensure flow is stable over the measurement will prevent measurements having to be repeated. Additionally, selecting an air sampling pump that has a good Ingress Protection (IP) rating will allow for easier decontamination, a process nearly as important as removing asbestos correctly in the first place.
Asbestos does not only pose a threat to trade workers, but those they encounter, should invisible yet lethal asbestos particles stick to their personal protective equipment and tools. Following stringent cleaning regimes can protect workers and their colleagues, family, and friends. All equipment must be thoroughly decontaminated to ensure there is no subsequent exposure or spread of asbestos. Choosing a high flow pump with a smooth body finish, free from small crevices, will allow for safer decontamination and cleaning. Modern air sampling pumps can also be monitored remotely with Bluetooth via a mobile’ app to check the sampling status, saving time checking pumps.
Basic awareness training is not enough
Asbestos monitoring has the power to save lives, but only when carried out correctly. Basic awareness training is not enough. Additional consultancy and training should always be acquired before carrying out asbestos removal to achieve the required level of competence and help keep more workers safe.
Tim Turney is Global Marketing Manager at Casella and graduated as an engineer from Queen Mary and Westfield in London. Since starting at Casella in 1998, Tim has been involved in the acoustics and air sampling industry, specialising in measurement and instrumentation technologies.