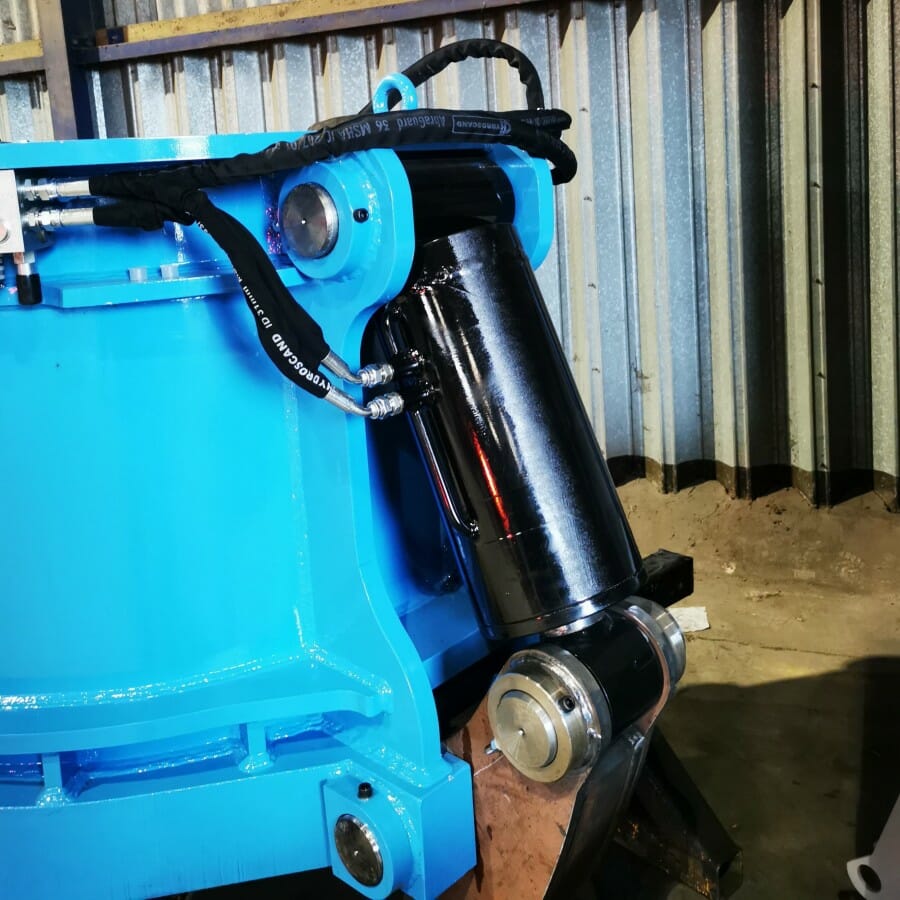
Hoses can fail for many reasons, from incorrect installation to general wear-and-tear.
In busy work environments, hoses can become worn down through day-to-day use or be damaged through operator error. Products can also develop faults if they haven’t been correctly installed or maintained, such as insufficient routing or incorrect swaging risking a burst hydraulic hose.
The environment in which hoses are used can also have an impact. Externally, covers can deteriorate or become damaged due to the working environment, causing a hydraulic hose leak. Internally, tubes can degrade if there are spikes in the hydraulic system or incorrect pressures are used, or if fluids become contaminated or too hot.
Careful product selection and proper hydraulic hose assembly are essential – ensuring the best product is being applied and in the correct manner for the machinery or method in use.
How can you minimise the risk of hose failure and/or prevent a burst hydraulic hose?
Risks can develop through incorrect hose installation and usage, stresses in the hose environment, or user error.
Hose installation & usage
Understanding what’s required of a hose and the stresses it will be subject to is central to reducing the risk of faults or failure. Different products have different tolerances for temperature, fluid flow, flexibility, and friction, both internally and externally.
Installing and assembling hose parts correctly is also key. Correct insertion depths must be met, and hoses should be cut or swaged properly, without risk of inner tubes becoming contaminated or worn down.
Hose environment
The environment in which a hydraulic hose is used and the fluids or gases running through it will also impact its longevity. External forces and internal stresses can degrade or damage the hose, causing sudden ruptures or gradual wearing. Maintaining the environment surrounding a hose is important to reduce risk, preventing ruptures or abrasions. Inner tubes can crack, erode or even wash out if subjected to high velocities, contaminated fluids, or dry or aged air. Understanding the impact of internal fluids or gases and their temperatures or usage pressures will minimise risk.
User error
How well a hydraulic hose is installed, used and maintained will hinge on the skill and understanding of operators. Ensuring workers recognise the importance of correct usage as well as the risks involved is key to minimising the likelihood of user error.
What are the risks?
Faulty hoses can cause operational, physical, and environmental hazards.
Internal degradation can risk a hydraulic hose leak, where inner tube plastics wash into connecting machinery leading to costly repairs and downtime. A sudden burst hydraulic hose could cause serious injury to workers while a gradual leak risk creating a slip hazard. If hydraulic hose replacement or repair is not prioritised, potentially hazardous fluids could reach waterways, risking environmental harm, significant fines, and reputational damage.
What are the benefits?
It’s also important to recognise the many benefits of good hose installation and maintenance. Equipment which functions well improves overall productivity, delivers operational efficiencies, and ensures worker safety. Investing in the right equipment and regular maintenance will pay dividends over time.
What to do when a hose bursts/fails (hydraulic hose repair):
Should a hose fail – whether through a leak, burst, breakage or disconnection – a partial repair or full hydraulic hose replacement may be required.
Broken or brittle inner tubes or coverings
Using a hose with greater resistance will prevent a hydraulic hose leak, as would applying a heat exchanger to manage fluid temperatures. Heat guards or shields can also protect hoses from external heat sources.
Worn or ripped covering
A worn covering suggests changes to the external environment will prevent further damage. Protective coverings can be applied, or hose guards, shields or clamps can offer additional protection to connections.
Burst connection or covering
A burst hydraulic hose may be caused by a faulty connection or if it has been flexed too much in one spot by repeated high-pressure cycles. Understanding what depth of fitting is required and how much flexibility or friction a hose can withstand will prevent bursts or disconnections.
Though there a number of factors that can cause a hydraulic hose to fail, many of the common causes are easily avoided through good product selection and proper maintenance. Investing in the right hoses and regular maintenance will reduce the risk of downtime to create long-term cost savings.
Our team can advise on the best products to optimize your processes, ensure good product durability, and reduce the risk of failure.
Contact Hydroscand for more information or to find the right hydraulic hose for your application. Visit www.hydroscand.co.uk or contact us at info@hydroscand.co.uk or on 0115 978 9759