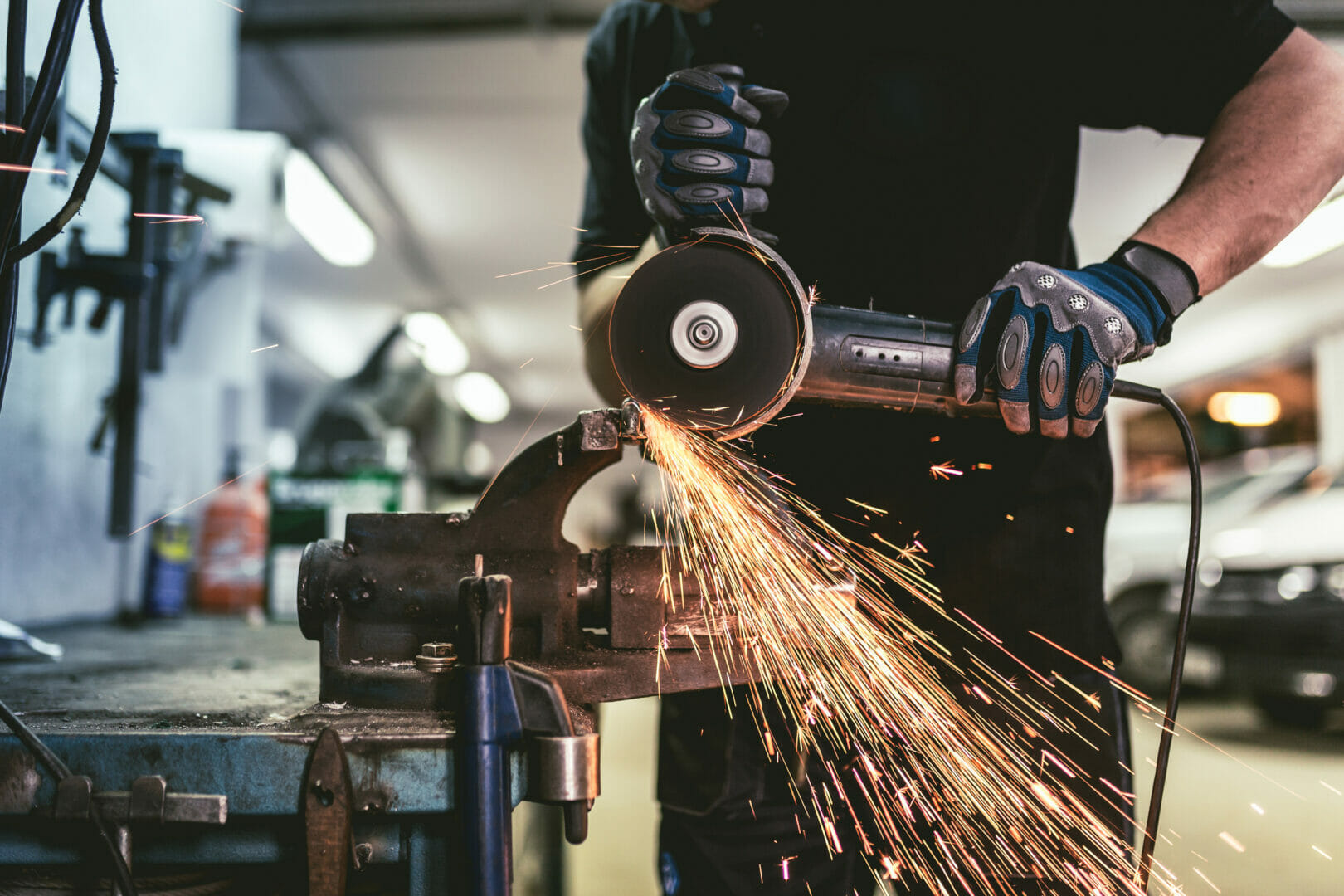
BY
Adam Ward, Category Manager for PPE and Hygiene, Brammer, Buck & Hickman
When it comes to maintenance and repair work, the use of hand-held abrasive tools can expose the operator to vibration which can increase the risk of Hand-Arm Vibration Syndrome (HAV). This can result in long-term injury and absenteeism.
How can employers manage and minimise the impact of vibration as much as possible without compromising on productivity and work schedules?
What is Hand-Arm Vibration Syndrome?
HAV is an industrial injury that is caused by continuous exposure to vibrations from handheld tools or types of machinery such as grinders, disc sanders and random orbital sanders, etc. Often damaging the blood vessels, nerves and tendons in the fingers, hand and wrist, HAV can be a disabling condition and can result in reduced sensitivity, strength and dexterity. Once these conditions take hold, they are irreversible, so it’s important to take appropriate early steps to reduce the risk of over-exposure to vibration.
Prevention is better than a cure
According to the Medical Research Council, nearly 5 million people are exposed to HAV at work. With vibration-induced disorders representing the fourth most common claim for compensation within the UK, it’s clear to see why the control of vibration is an important consideration within the workplace.
The Health & Safety Executive (HSE) offers employers important guidance on how this should be achieved under ‘The Control of Vibration at Work Regulations 2005’. These regulations highlight the ways to eliminate, reduce or substitute tasks involving high levels of vibration.
The regulations also set out a maximum acceptable acceleration level of 5m/s2 for an average vibration exposure over an eight hour workday. In addition, if staff are exposed to vibration levels above 2.5m/s2, employers must introduce organisational and technical measures to reduce exposure, along with a health surveillance program to detect and respond to early signs of damage.
Control the level of vibration
When it comes to the control of vibration in the workplace, there are various questioned that need to be addressed.
Firstly, is the tool or process well maintained and working correctly? How long and how often is the equipment used? Both questions are important as they can have an impact on how well the equipment performs and how much pressure and time is spent performing a job. If an abrasive tool isn’t cutting as fast as it should, the job could take twice as long, which will increase vibration exposure.
You will also need to consider how the equipment is being operated; for instance, is it affecting the operator’s posture, or are they working for long periods in cold, damp conditions? Again, both factors can increase the risk of HAV.
Also, are you looking at the complete picture? Don’t forget, each process adds to vibration exposure so if your employee is using two or three different tools in a day, each tool has its exposure, action value and its level of vibration, therefore each process must be added to give a cumulative picture of an entire working day and the limits permitted.
Once you’ve taken these questions into account, various practical methods can be undertaken to minimise vibration. Where possible, seek to remove or reduce the use of vibrating tools or work processes; for example, use alternative non-vibrating methods such as jigs and clamps to avoid or minimise the need to hold vibrating tools or workpieces, and automate tasks where possible.
Organising work schedules and rotating staff can also limit the amount of time each worker spends exposed to vibration.
Tool selection is another factor that needs to be taken into consideration when it comes to reducing the level of vibration exposed by operators. Are they the right size and power for the task? Reducing the weight of a tool and the distance it must be carried can reduce HAV injury risks, but an underpowered tool may encourage operators to use greater pressure, or force them to hold the tool for longer, increasing pressure.
Selecting the right abrasive is an essential part of reducing tool vibration. For a lot of people, abrasive discs and wheels all look the same, but don’t let looks fool you! The development of abrasives has exploded during the last decade and manufacturers now offer abrasives of various types and grit sizes in different types of substrates for different applications.
What tool features should you look for?
Firstly, we need to consider the quality of abrasives, as this can be extremely variable. Always ensure that products are clearly labelled with maximum operating speeds, shelf life and compliance with relevant manufacturing standards. Purchasing low cost abrasive products might seem like a good idea, but when you consider the risks of exposure and subsequent staff absenteeism, not to mention the cost to regularly replace products, it’s going to cost a lot more money in the long run.
Secondly, it’s important to look for abrasives that cut faster and require less operator pressure. The use of high-performance abrasives can reduce overall vibration by allowing tasks to be completed faster, with less operator trigger time. This can then be turned into a quantifiable cost-saving. In addition, this can also help to reduce operator fatigue which can play a significant part in overall productivity.
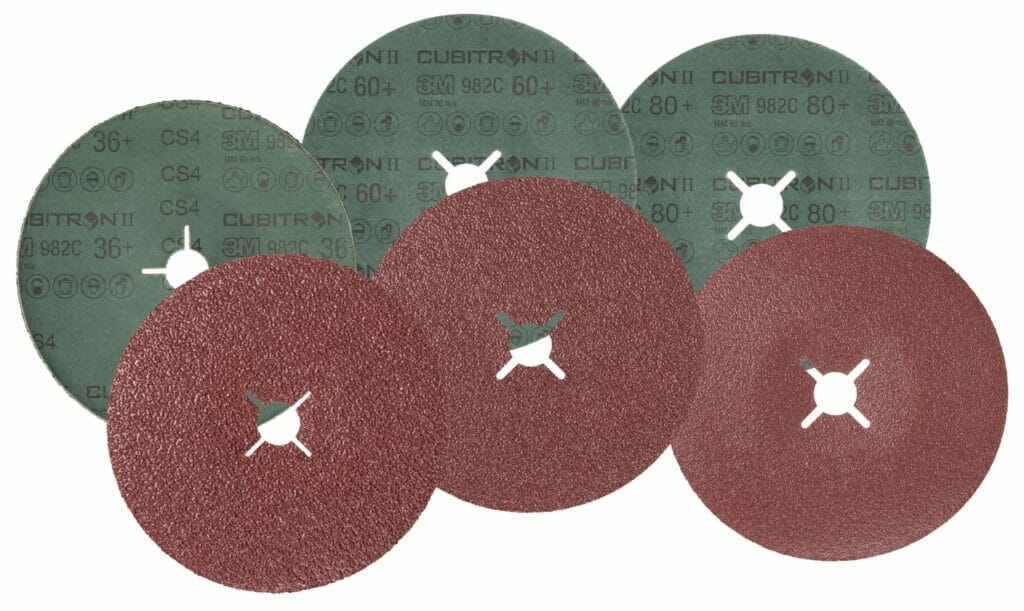
When it comes to abrasive products, there isn’t a “one size that fits all” so it’s important not to opt for the simple, generic approach. Coated abrasive belts can produce less vibration than bonded wheels on fixed machinery whereas bonded wheels can be replaced by fast cutting and long-life fibre discs on hand-held angle grinders.
Therefore, it is also important to consider the grain used in the abrasive product. Conventional ceramic abrasive grain is irregular and blocky in shape which can occasionally present issues. Instead of a clean, machining action, the grain tends to “plow” through the metal, causing heat to build up in the workpiece and the abrasive, which can result in a slower cut, shorter belt life and undesirable effects.
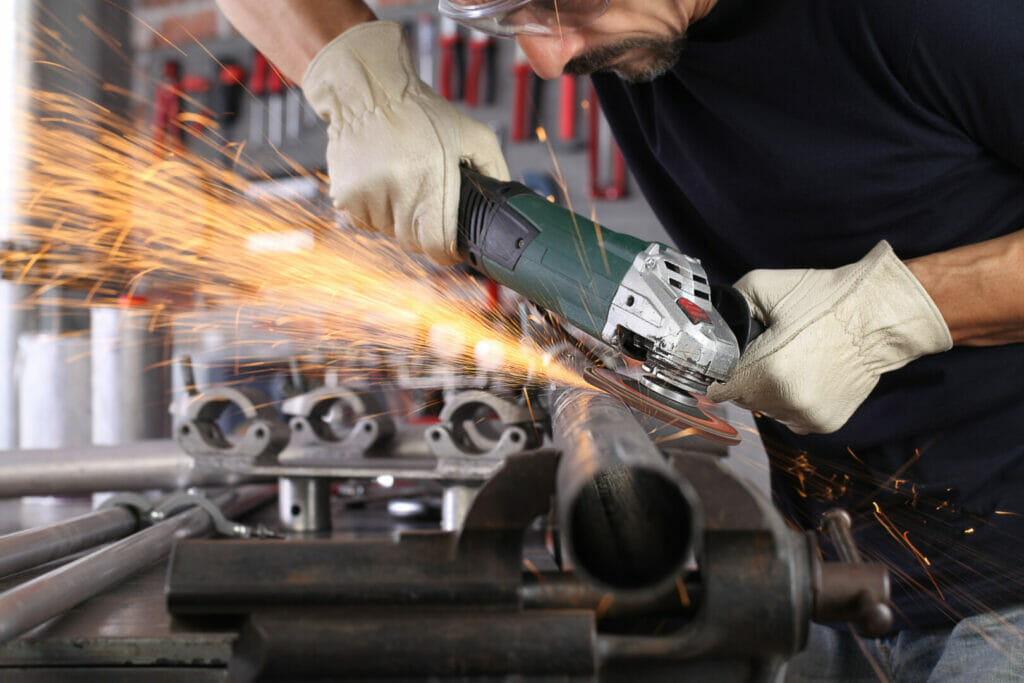
An abrasive that stays sharp is key. To address this issue, the 3M™ Cubitron II range of abrasives, available from Brammer Buck & Hickman, feature a revolutionary precision-shaped ceramic grain technology. As the triangular-shaped grain wears, it continually fractures to form sharp points and edges that slice through metal, wear evenly, and provide long life and consistency at any grinding pressure.
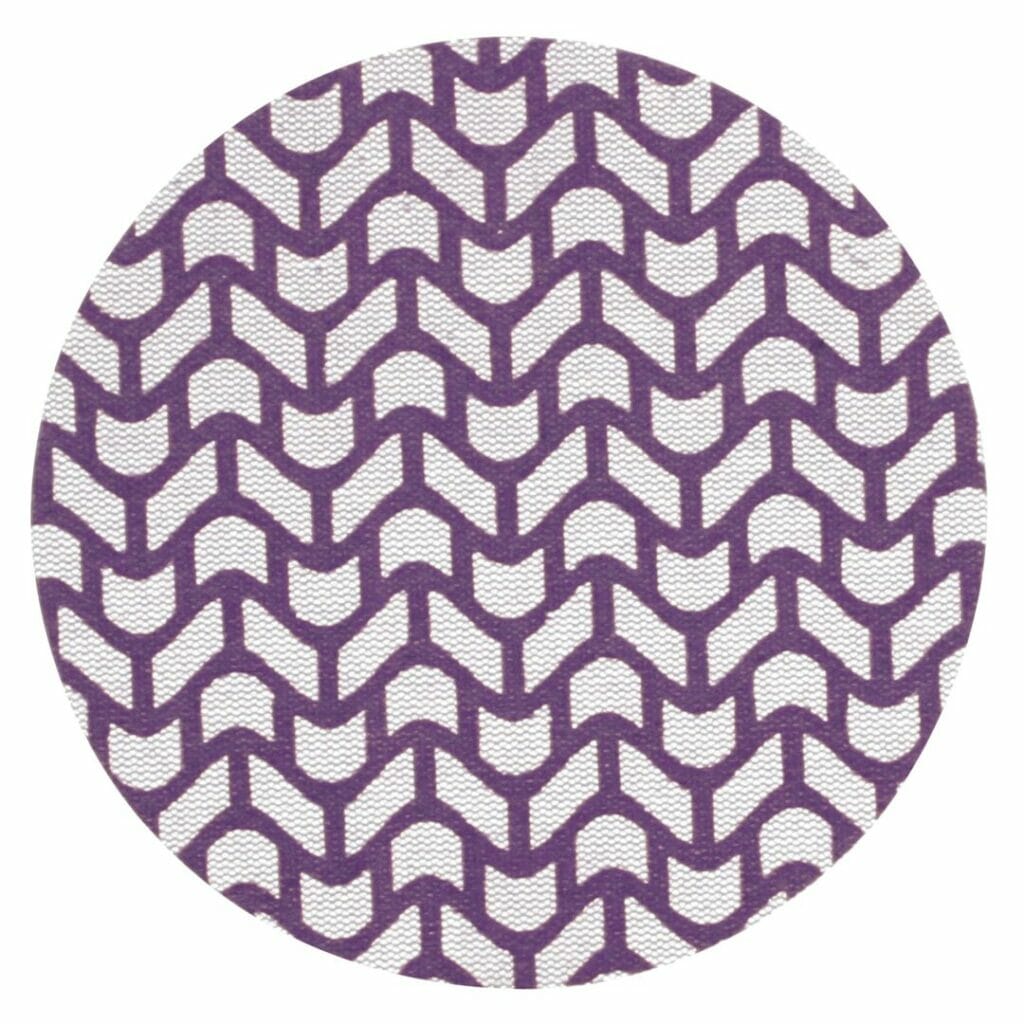
Conclusion
Without a doubt, HAV can have serious consequences for both the operator and the employer and as a result, there needs to be a fine balance between safeguarding the workforce and maintaining productivity. Looking at ways to reduce or substitute tasks involving high levels of vibration is important, with the most effective being to consider what tools and abrasive products are being used.
For more information on the regulations visit: at http://www.hse.gov.uk/vibration/hav/regulations.htm. The full text of the regulations can be accessed at http://www.opsi.gov.uk/si/si2005/20051093.htm.
Brammer Buck & Hickman, Europe’s leading distributor of Maintenance, Repair, and Overhaul (MRO) products and services, is an appointed national distributor for 3M. For more information from its acclaimed range of abrasives, tapes, and adhesives, please visit: https://uk.rubix.com/en/3m-all/c-UK_3M-All-Products