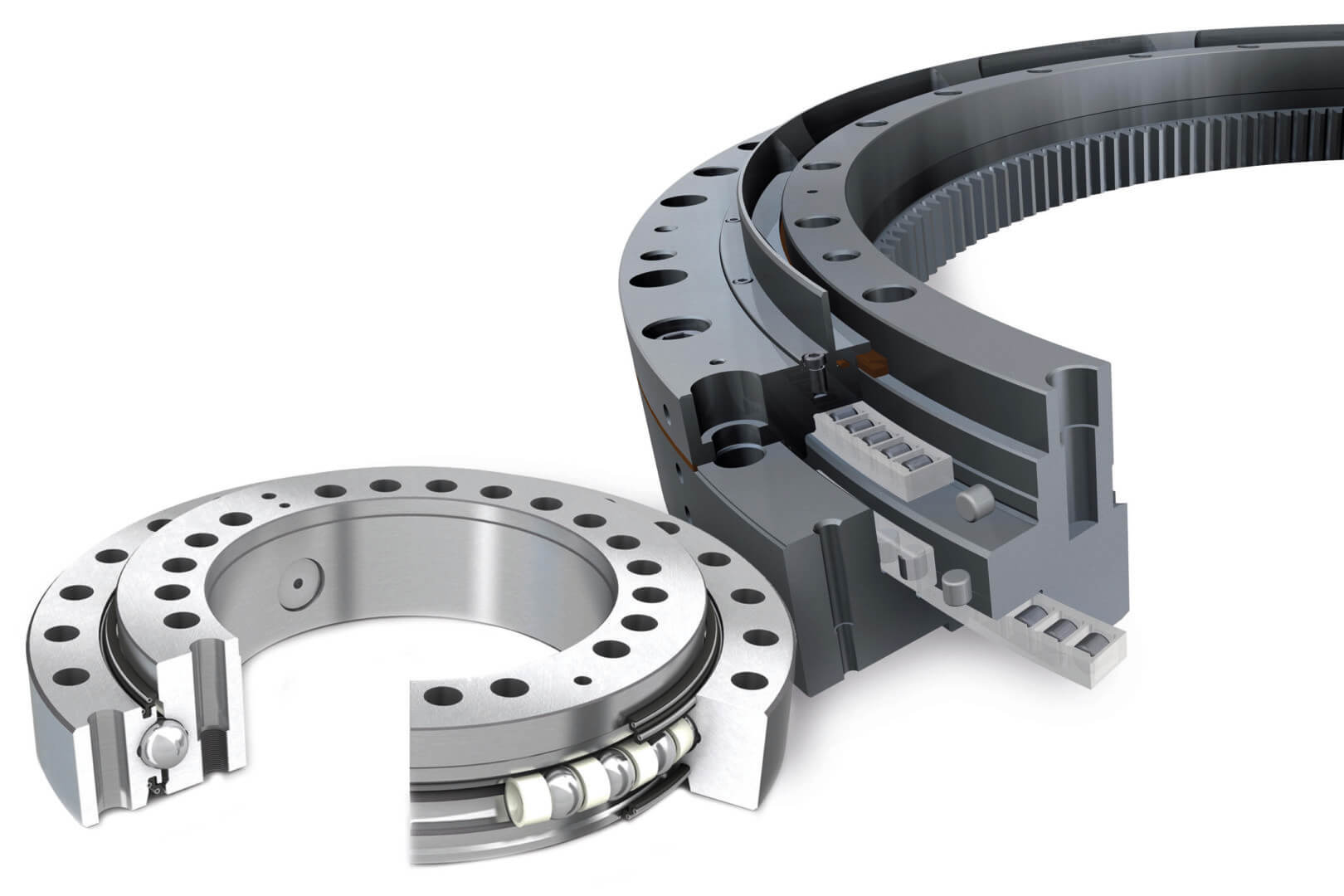
Bearings keep machinery moving. Wherever there is a machine or vehicle that has rotating parts, you will find bearing units. Across all industries, bearings are one of the most often replaced components, but in construction all the more so due to the exceptionally harsh operating conditions. Here, bearings face multiple challenges, from ingress of dirt and dust, through to very heavy loads and frequently working in extreme temperatures.
As with any component, you want your bearings to provide long, trouble free performance. To maximise lifetime expectancy, the bearing must be correctly installed, lubricated and maintained. However, regular lubrication and maintenance is problematic when it comes to construction sites as downtime for maintenance is very expensive, and safety is a running concern with such heavy equipment at hand.
Selecting the correct bearing is therefore essential to ensure reliable, long life. Here we look at the top challenges faced in this sector and suitable bearing options to meet those challenges.
Operating Conditions
Construction sites are notoriously wet and dusty and are often impacted by extreme temperatures. Furthermore, the machinery and vehicles in operation are heavy duty, placing substantial loads on to the bearing units.
In this environment, open bearings quickly become damaged from ingress of dirt. Using proper sealing solutions such as sealed bearings and shaft seals is therefore essential. Sealed bearing units are initially lubricated and then sealed, preventing dirt for entering and mixing with the lubricant. Specialist sealing solutions have been developed for this sector, including SKF’s Three-Barrier Solution which consists of a sealed spherical roller bearing, bearing housing with labyrinth S seals and a specially formulated lubricant to act as a contamination barrier.
These three barriers protect the bearing from contaminants, leading to extended bearing service life on average three times longer than standard open bearings. It is particularly well suited to conveyor systems.
To function in applications where heavy loads are the norm, you want a bearing that is both hard and tough. In the past, hardened steel did not have all of the necessary properties to make it suitable for use, but new heat treatment processes have been developed to remedy this. Also, consider both axial and radial loads when choosing your bearings. Double row tapered roller bearings are a good option they accommodate combined loads and can locate a shaft axially in both directions with a precise axial clearance or preload.
Health & Safety
Health & safety concerns are key in construction. Working with heavy equipment makes injuries more likely to be potentially life changing or threatening.
The main cause of casualties in the construction industry occurs during maintenance and repairs, with maintenance on conveyors being one of the major culprits. Every time a piece of equipment fails, safety is compromised. Using optimised bearings, sleeves, housings and seals can improve machine reliability and ease of assembly and disassembly. SKF ConCentra Roller Bearing Units (ideal for conveyors), for example, come “shaft-ready”, i.e., they simply slide onto the shaft and are locked into place by tightening the screws. It’s fast – requiring far less time and skill to install than a split pillow block housing assembly – and helps provide proper alignment while reducing the risk of assembly-related mounting errors.
Lubricant is essential to keep moving parts in optimal condition, but lubricant is a hazard in itself. If dripped on to the floor during application, or fallen from the machine if too much has been applied, lubricant becomes a slip hazard. Lubricants can also be an accelerant, so a potential fire hazard. Use of an automatic lubrication system decreases quantity of lubricant, which reduces probability of leakages and also reduces the need for workers to go to hazardous locations for relubrication. Ensure suitable seals are used to reduce maintenance requirements and leakages. If possible, opt for sealed bearing units to remove the need for relubrication and potential spills altogether.
Sustainability
At a time when the world is looking to limit its energy usage and impact on the climate, pressure is mounting on the construction industry to reduce overall environmental impact.
Poor bearings performance can directly affect energy usage. Although the amount of energy per bearing is relatively small, when you consider how many bearings are used in machinery on a given site, it starts to mount up. Choosing the right product makes for a more energy efficient approach. Look for those that have lower operating temperatures and vibration levels.
Ensuring product is correctly fitted also has a part to play. Misalignment can lead to friction and vibration which can significantly increase energy consumption, plus the risk of premature failures. Shaft and belt alignment tools are readily available that allow customers to increase their machine reliability through easy to use and accurate alignment. Other options include selecting products that don’t require realignment, such as SKF Cooper Split Spherical Roller Bearings that do not require the drive coupling or the cantilevered drive to be dismounted to replace the bearing; these bearing types are easily and safely replaced in situ.
Bearings may not be the most expensive part of your onsite machinery, yet they are in widespread use. Apply the 3Rs: Reduce, Reuse, Recycle.
Reduce the number of replacement bearings you use by using good quality bearings that have been designed to both do the job at hand and operate in the appropriate environment. This will ensure product longevity. Reduce the amount of lubrication you use through employing automated lubrication systems or sealed bearings.
When it comes to Reuse, some manufacturers offer a remanufacture service which can significantly prolong bearing service life, as well as reduce cost and lead times. Bearing remanufacturing can significantly reduce carbon emissions, consuming around 10% of the energy of making a new one.
Recycle bearings at end of life. Not every part of a bearing can be recycled and not every manufacturer can do this. Check to see if your supplier offers this service.
Brammer Buck & Hickman, aRubix group company, is Europe’s leading authorised bearings distributor, selling over 100 million bearings annually from the largest, most comprehensive bearings range and stock.