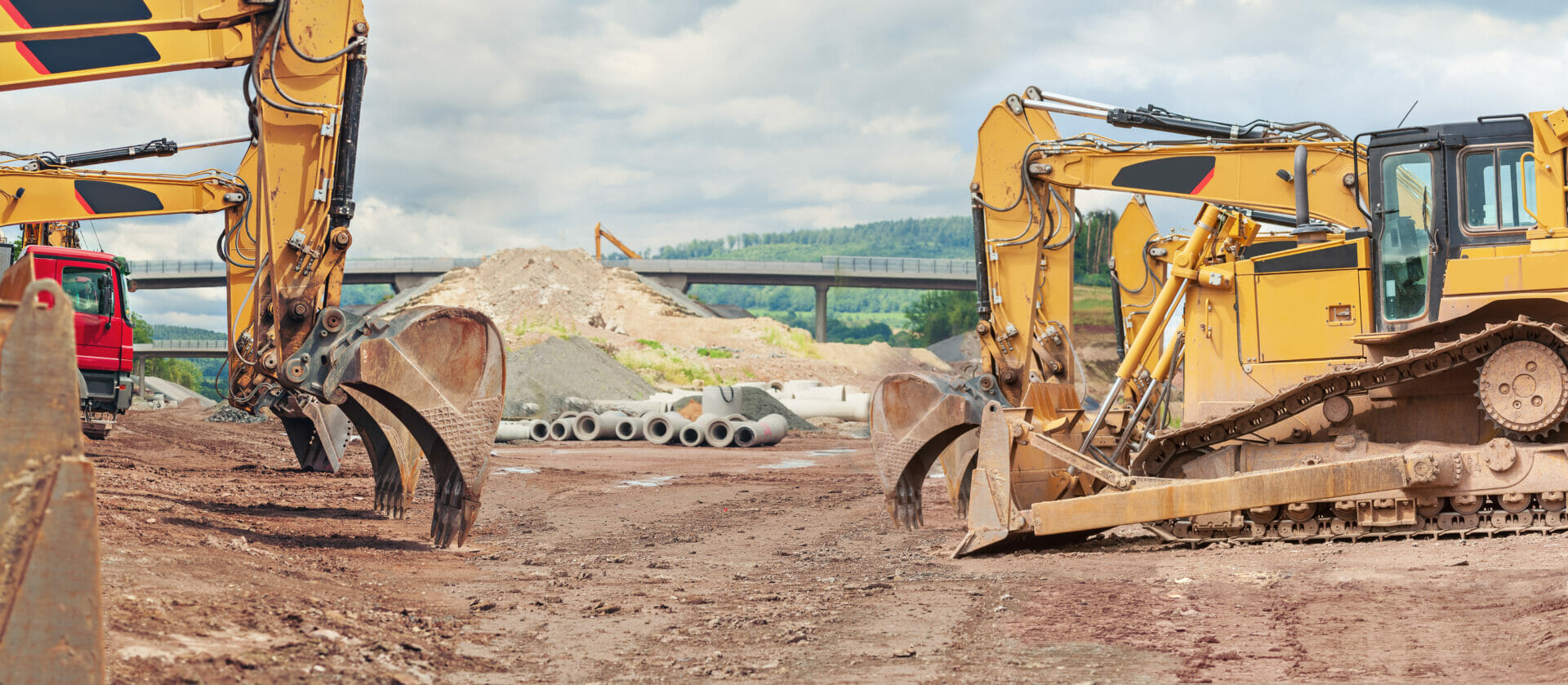
For those who work in the construction industry the risk of exposure to hazardous gases is all part of the working environment. In 2019/20 there were 8 fatalities and more than 200 non-fatal incidents related to harmful gas exposure in the UK, compared to that of the previous 2 years.
It is evident that volatile organic compounds (VOCs), which are emitted as harmful gases, pose a significant risk to employee’s health and safety within the construction industry. Minimising the risk of harm due to dangerous gases is a problem that demands urgent attention.
Construction applications that apply or generate hazardous gases
The construction industry uses several VOCs and hazardous chemicals such as adhesives, paint, and flammable gases which are stored on site in tanks, cylinders and containers. If these items are incorrectly stored or damaged during transit, they can pose a hazard to site personnel including the risk of asphyxiation or explosion. In the UK, the Health and Safety Executive (HSE) sets out guidelines for the safe storage of hazardous chemicals and gases, which includes guidance for correct ventilation, compatibility with other stored materials, stacking and storage layout, on-site transportation, container maintenance, and containment of leaks and spills.
Welding is a construction activity that uses hazardous flammable gases, such as acetylene, argon, hydrogen, and propane. The most common type of on-site welding is MIG or TIG welding which often uses a carbon dioxide and argon mix. During welding activities, fumes are released as the metal is heated above its melting point, causing evaporation and condensation into fumes. In addition to metal particulates that may affect long term health, welding fumes may contain nitrogen oxides, ozone, hydrogen chloride, phosgene, and carbon monoxide, which makes them a potential risk to onsite personnel, especially in confined spaces. Appropriate ventilation is essential if some serious health risks are to be avoided. In 2018, the International Agency for Research on Cancer (IARC) classified welding fumes as a carcinogen, based on strong evidence. Therefore, welding fumes need to be carefully monitored and controlled to ensure health and safety of construction workers.
All construction projects involve some degree of land trenching and excavation. As well as the risk of cave-ins, digging activities can also result in the release of toxic gases when gas pockets are breached, or sewer or gas pipes are accidentally ruptured. Additionally, exhaust gases from machinery can accumulate to dangerous levels and reduce the oxygen levels in the trench or hole. Some common gas types including carbon dioxide are far denser than air and can collect in depressions, holes and trenches, where they may cause their own health effects in addition to reducing the oxygen intake of anyone operating in the hole or trench. Some flammable gases common on building sites are even denser and can pool unseen in the bottom of trenches where they may be ignited by a hot surface or a spark.
During land clearing activities, the chances of a gas pipe rupture is increased. Underground pipe location technology has improved in recent years with the application of electromagnetic and radio detection tools, but these methods are never fail-safe. If a gas pipe rupture goes unnoticed, the risk of explosion and consequent harm to personnel increases considerably.
Demolition activities often take place in hazardous environments such as old industrial buildings. The risk of unintentionally releasing hazardous gases such as carbon monoxide, methane, or hydrogen sulphide is high during demolition works.
Managing the risk of hazardous chemicals
In the United Kingdom, the Institution of Occupational Safety and Health (IOSH) has released guidance on managing the risk caused by hazardous chemicals, including VOCs. The four main steps that IOSH identifies as crucial to managing the risk of hazardous substances, including dangerous gases, are:
- Understand the health consequences of accidental exposure
- Ensure safe handling, storage, and use of the chemical
- Apply safety measures to minimise exposure risk and protect workers
- Establish robust emergency procedures.
An important part of the process is to undertake a thorough risk assessment. However, unlike a typical risk assessment of controlled risks, you should also assess any uncontrolled risks to help identify potential exposure to hazardous gases. For example, in the case of on-site excavation, it is advisable to assess the risk of releasing gases from an underground pocket, such as methane gas. A thorough risk assessment will help you to create a risk mitigation strategy and emergency response procedure. For instance, you may decide to fit excavation machines with methane gas detectors as a control measure to mitigate the risk of exposure or explosion.
Global focus on construction health and safety
Over the past three decades, there has been significant global action to improve health and safety standards for construction workers. The International Labour Organization (ILO) has been instrumental in improving health and safety in the construction, including reducing the risk of exposure to hazardous chemicals and gases. In today’s world, we have technology at our disposal that can do more than provide basic provisions and preventative measures. Gas detection technology is sufficiently advanced to provide early warning of the presence of dangerous gas and prompt an emergency response.
Gas detection – reducing the risk of hazardous gas exposure
Gas detection is an important control measure to help reduce the risk of harm to construction workers. Gas detection can be applied at various stages of the construction process, these include the design and planning phase, underground detection, rupturing buried services, above ground construction activities and underground construction activities. All of which create a high risk of toxic gases building up or being released into the environment. Gas detection reduces the risk of hazardous gas exposure from the design and planning stage to when the construction work commences, there is an increased risk of carbon monoxide.
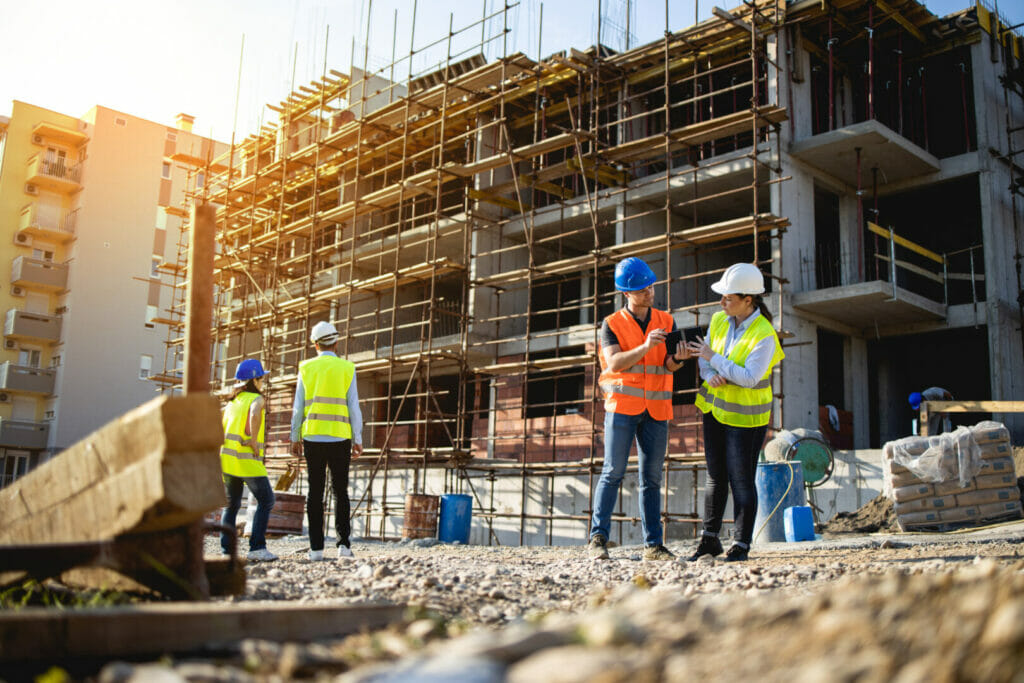
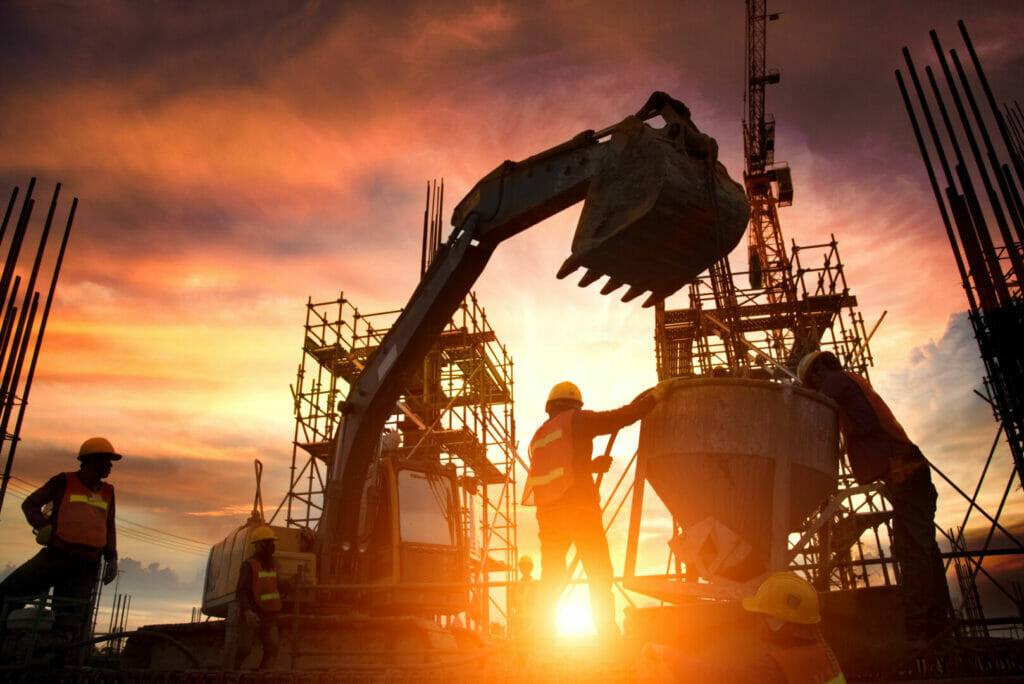
Gas detection technology
Gas detection is a necessary control measure to meet health and safety standards and comply with regulations in the construction industry. Crowcon offer a wide range of gas detection products to help you improve construction site safety. Our personal portable gas monitors offer versatility and flexibility in use and again if heightened gas levels are detected can activate alert systems, enabling workers within construction environments to take immediate appropriate action.
Our fixed gas monitors provide constant readings from a specific location and therefore can be implemented throughout a construction site for a cross section of monitoring reports. Site-wide warning systems offer data from several areas and can be analysed within a central control room and across the safety network. If abnormalities are detected, automatic alerts and safety measures can be activated to provide safety fall backs, alongside options to remotely shut down an area and isolate hazards.
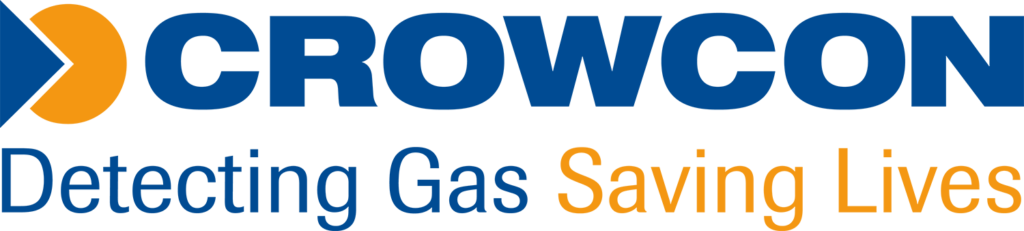
For more information about gas detection solutions for the construction industry visit www.crowcon.com or email us [email protected].