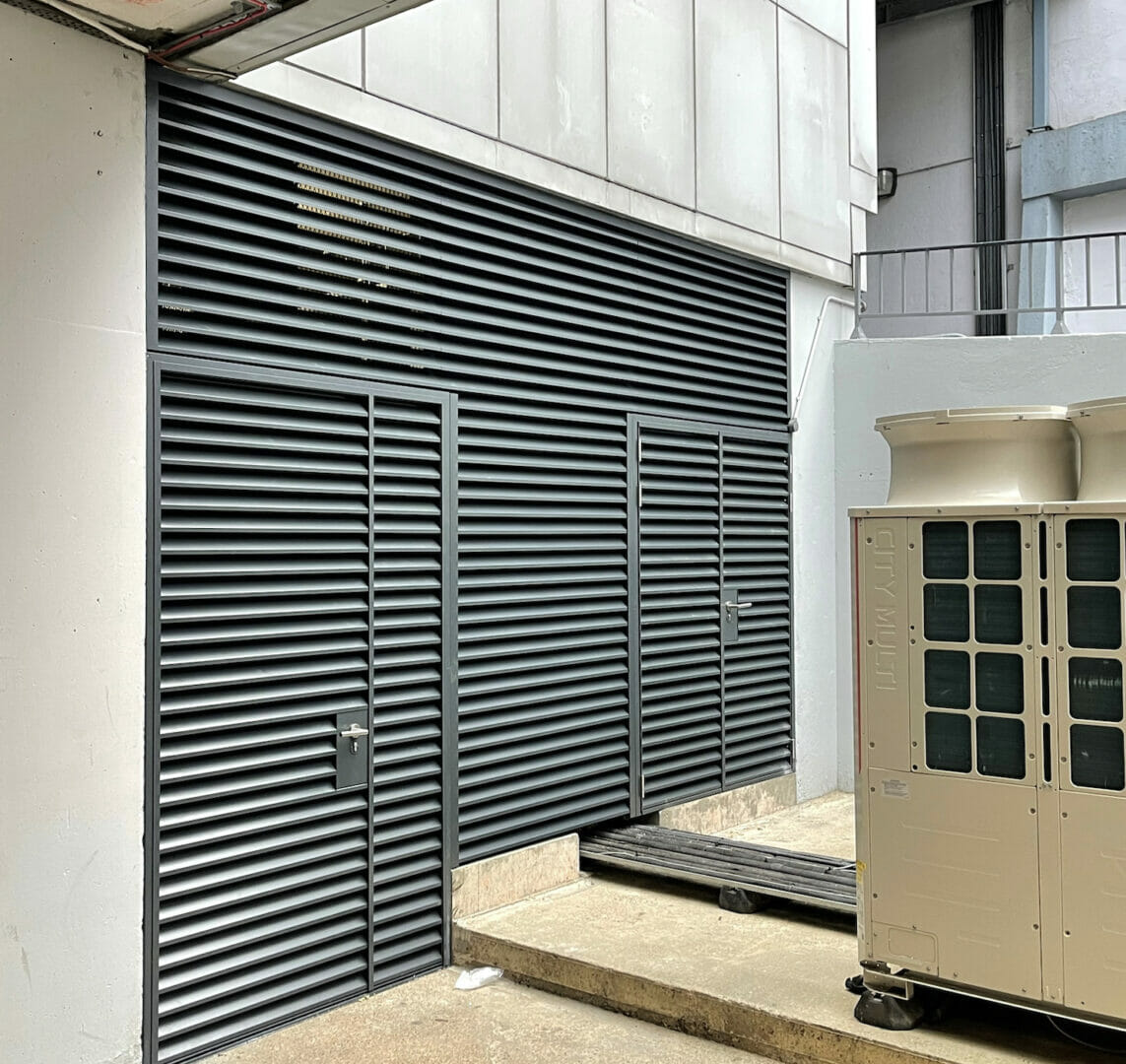
Design expertise behind the scenes is giving work life in the heart of London a light, bright and safe environment.
Adeline Properties commissioned NGA Architects to refurbish and upgrade the 10-storey, 60,000 sq ft Waverley House, Soho. The challenge for the design team was to optimise a light, inspirational feel and bring the interior and office space up to the high standard demanded in a highly urbanised location. The only suitable and available space for siting of new building services plant was in the basement at the rear of the building. That location was further hampered by varying ground levels, protruding pipework and the need to make the plant- and building- secure.
Building services consultant the Consultus International Group advised protective insulated louvres be integrated into the façade to protect the a/c and hydro plant, and recommended Gilberts Blackpool to design, manufacture and install the plant screening.
The brief involved provision of adequate natural ventilation for the primary gas main in conjunction with thermal optimal efficiency of the plant behind whilst including access apertures to facilitate maintenance. The screen also needed to accommodate various pipework penetrations, protect against extreme temperatures and airborne particulates and pollutants.
Gilberts’ in-house team designed a special support structure to fix the louvre screen in place and address the stepped ground levels. The screen itself was engineered using Gilberts’ WGK75 louvre system, being purpose-designed for site-assembly whilst providing up to 50% net free ventilation area.
Mullions up to 1.9m tall were fabricated to support the louvre blades, clipped into place on site to enable precise positioning, especially around penetrating pipework. Plenum box sections designed into the screen optimised air circulation as part of the natural and mechanical ventilation strategy. Non-combustible insulated blanking plates were incorporated to moderate noise and temperature variation through inactive areas. A pair of double door sets were included: one set providing access for maintenance and plant removal split 1/3: 2/3 with internally opening leaves and open area for gas meter ventilation; the other set were outward opening, for access to isolation valves.
The whole assembly was complimented by a secondary support system using 4” x 4” aluminium box section, finished as the louvre screen, delivering appropriate support for the louvres, doors, insulation and plenum assemblies.
“Whilst not a big project, Waverly House was challenging,” explained John Hanger, Gilberts’ Area Sales Manager. “It was a complex screen that had to meet a variety of requirements- to protect the building services plant from the elements whilst enabling ease of maintenance, improved plant area access and security. The basement was the only suitable location for the plant on/around the building. That site added its own challenges, being constrained on working space and having to ‘step’ the screen to provide a flush fit to the ground.”
Added Michael Collins, NGA project architect, “The consultants put forward Gilberts. The finished louvre helps bring the basement into line with the smart, clean ambience we have aimed for throughout Waverley House.”
Gilberts’ range of kitform and factory-assembled standard architectural, weather protection and acoustic louvres are just part of its range of solutions that have established it as the UK’s no 1 independent commercial air movement supplier. Gilberts’ louvres have been installed in locations as diverse as Wimbledon no 1 Court, National Composites Centre, Blackpool FC, Papworth Hospital and Museum of London (formerly Smithfield Market).
Family owned, the company has a 60 year heritage of innovation, operating from a 95,000 sq ft facility in the Northern Powerhouse of Lancashire.
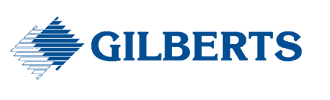