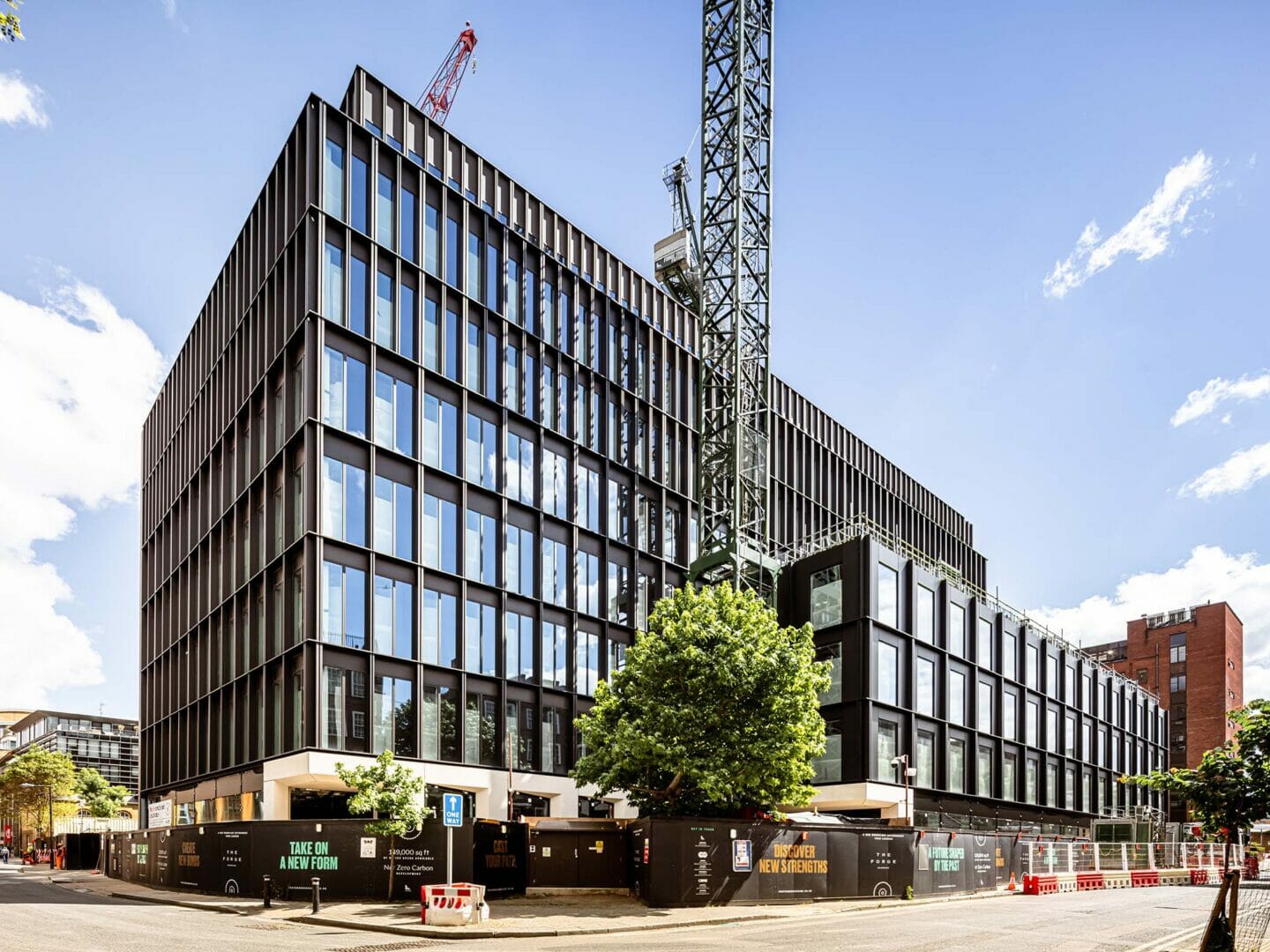
by Wojciech Brożyna – MD of Aluprof UK
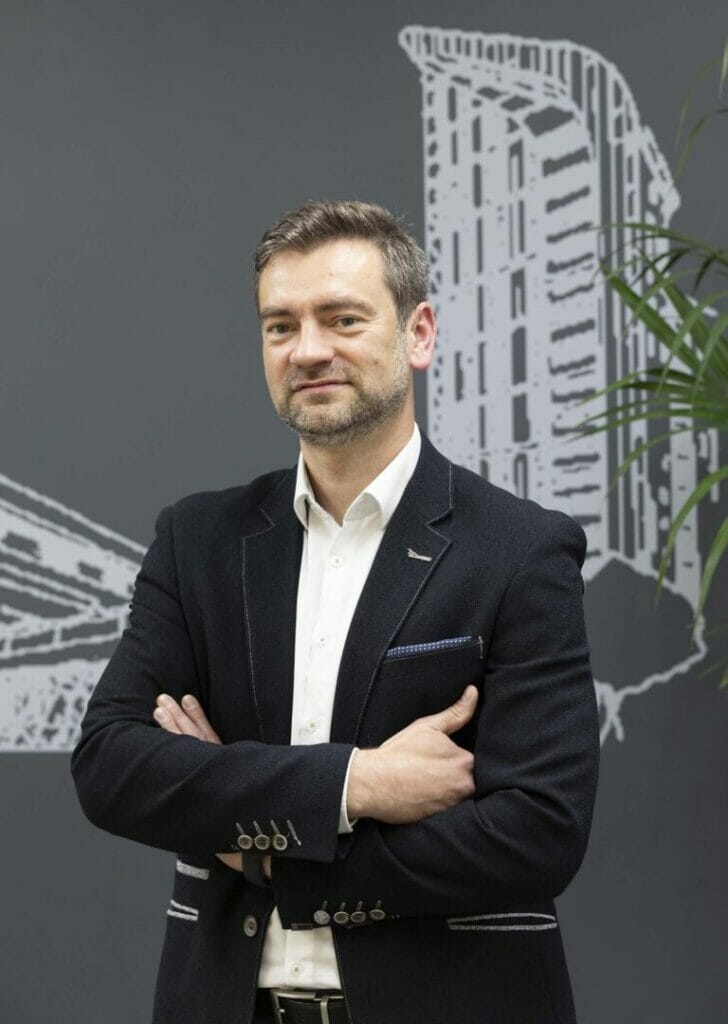
Many people in the Construction Industry still believe that BIM is just a modern design tool, but BIM is much more than this. Whilst design is certainly an element of BIM, collaboration is a key element, from inception through to completion of a project, and beyond. Collaboration across the design team, particularly at the early design stages both reduces risk and maximises value. A detailed BIM design forms a ‘single source of truth’ which de-risks the entire construction programme.
According to MacLeamy (2004) who plotted a simple graph of project time and project effort, it can be seen that the influence on the project design is high at the early design stages, whilst project changes further down the project timeline entails more effort and cost. MacLeamy argued that completing the design earlier in the construction programme reduced risk and cost by negating design changes later in the programme. An early BIM model using high quality, virtual BIM objects assists final design sign off earlier in the construction cycle.
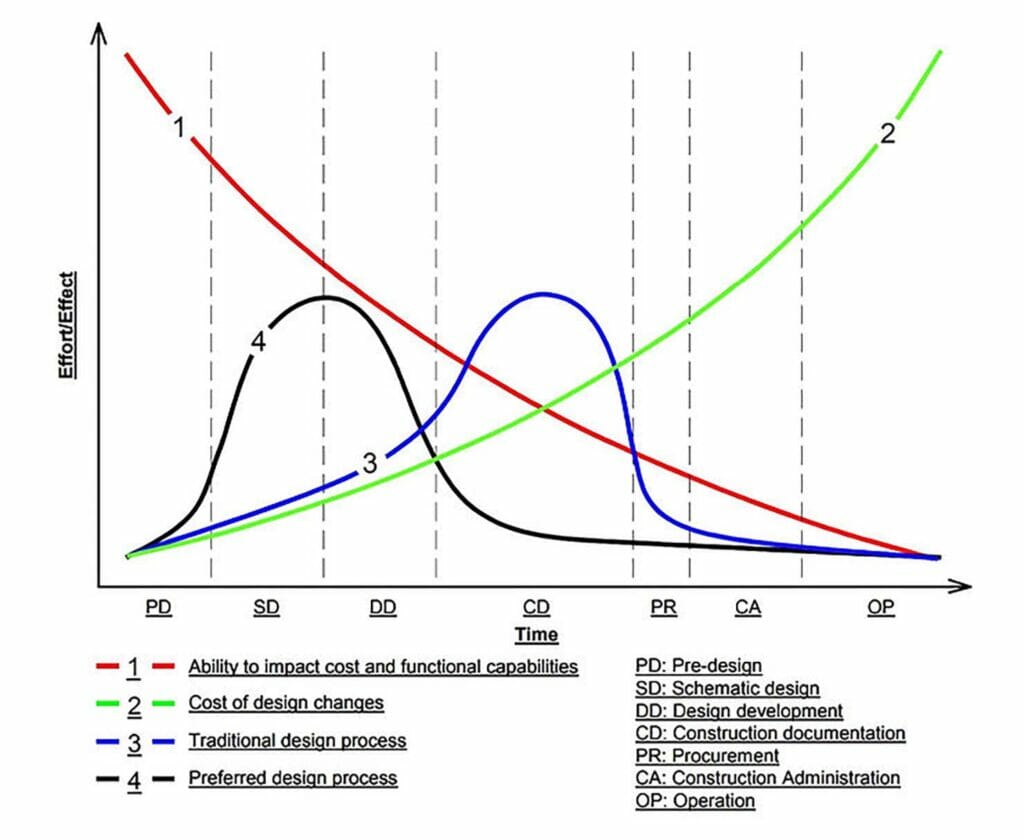
BIM has been with us for some years now, so it is far from a new concept, but helps us in developing new methodologies for construction, new methodologies which help us reduce carbon in construction. According to Transparency Market Research, in 2025 the Construction Industry will generate as much as 2.2 billion tons of waste annually which is about 50% of all global solid waste. The Construction Industry has to move from this linear construction process to a circular construction process where buildings can be deconstructed and rebuilt using some or all of the same parts, or materials recycled back into buildings. A growing number of architectural practices globally are designing ‘temporary’ or ‘deconstructable’ buildings that fall into the circular construction methodology.
In the UK a recently completed project in London, the Forge, aspires to be the first commercial building constructed and operated in line with the UKGBC’s net zero definition and energy reduction targets. It comprises two new office buildings and a public courtyard. Located on Sumner Street, The Forge is a Landsec office development located just behind Tate Modern in London and utilising BIM at its core is one of the most innovative construction sites in London, pioneering several new construction methods fit for the decades ahead.


Breaking new ground, the project is be the world’s first large-scale office scheme built using a standardised “kit of parts”, in an approach known as ‘platform design for manufacture and assembly’ (P-DfMA), which applies the advances made by the Manufacturing Industry to construction, this would not be possible without BIM. Aluprof are delighted to have been invited to take an early design role in developing a unitised facade system that meets the P-DfMA specification pioneered by architects and engineers Bryden Wood. Construction is led by Sir Robert McAlpine and Mace, working together in an innovative joint venture (JV) partnership.
Working with BIM essentially creates a 3D ‘digital twin’ of the building project and it doesn’t stop there. There are a further four ‘dimensions’ that are added, ‘4D’ Time, ‘5D’ Costs, ‘6D’ Sustainability and ‘7D’ Facilities Management. In effect, the BIM model carries all the data for the building, from the building programme through to eventual deconstruction. Any one element, such as the facade, falls into each of the dimensions of BIM, so the more detailed BIM models that can be obtained from suppliers, the greater efficiency is realised.
Finally, automated construction would not be possible without BIM as some of our building methods become automated, built by, or checked by ‘robots’. Yes, this could be the dawn of the robotic ‘Clerk of Works’. During the construction phase of a building, robots are being utilised to laser scan and monitor what has been built offering dimensional accuracy as well as monitoring the programme of works. This ‘real time’ analysis ensures that any potential problems are highlighted at very early stages, saving both cost and time.
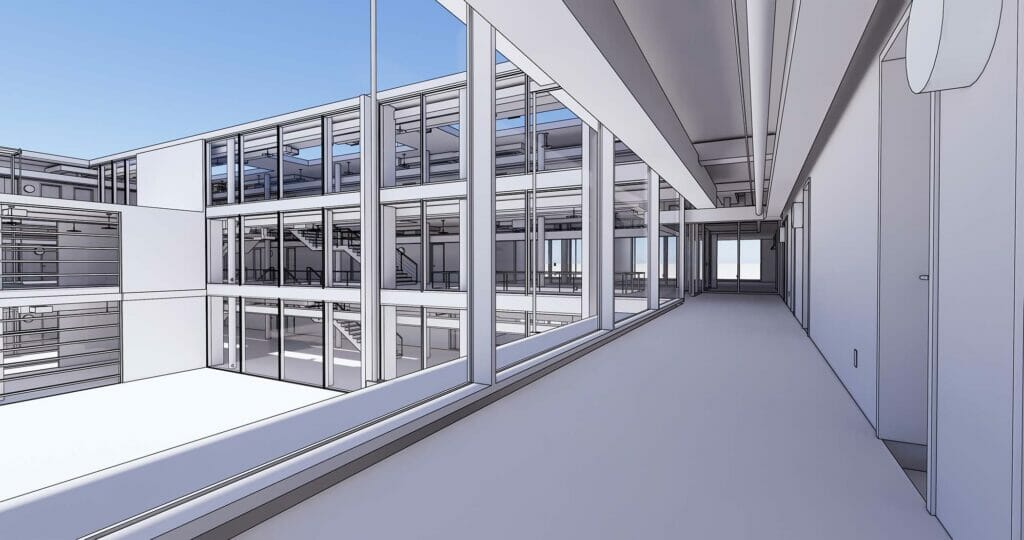
With its acclaimed BIM Academy, Aluprof continues to pioneer innovative solutions in partnership with specifiers across the globe. With a huge library of models available to architects and engineers, Aluprof are constantly adding new models for standard and bespoke designs helping clients and developers obtain efficient and sustainable buildings.
Aluprof UK are proud to supply facade systems to a wide range of new and refurbished construction projects across Great Britain and Ireland, with Head Offices in Altrincham in the North West and with an architectural specification support office in the Business Design Centre in London, the company has rapidly grown their specification influence in the UK with their high-performance architectural aluminium systems. Further expansion of the company’s headquarters in Altrincham now provides specifiers with meeting facilities and an extensive showroom of commercial systems to view.
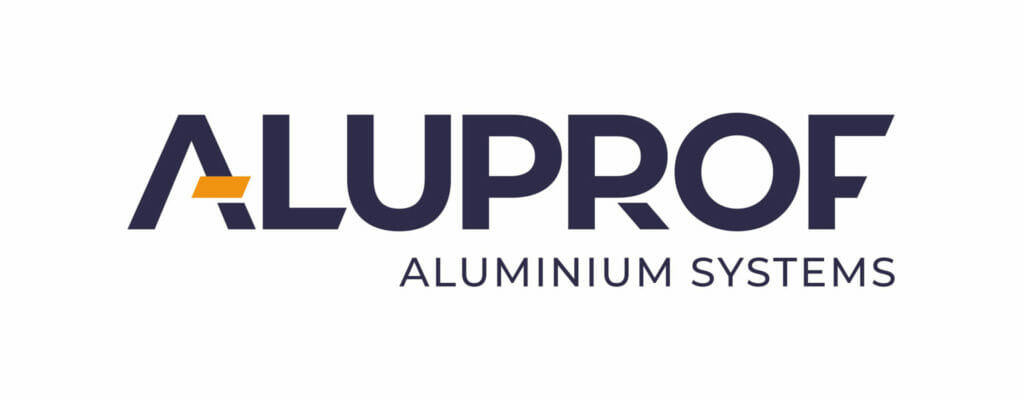
Further information is available on the company website at aluprof.co.uk or direct from their UK head office in Altrincham on 0161 941 4005.