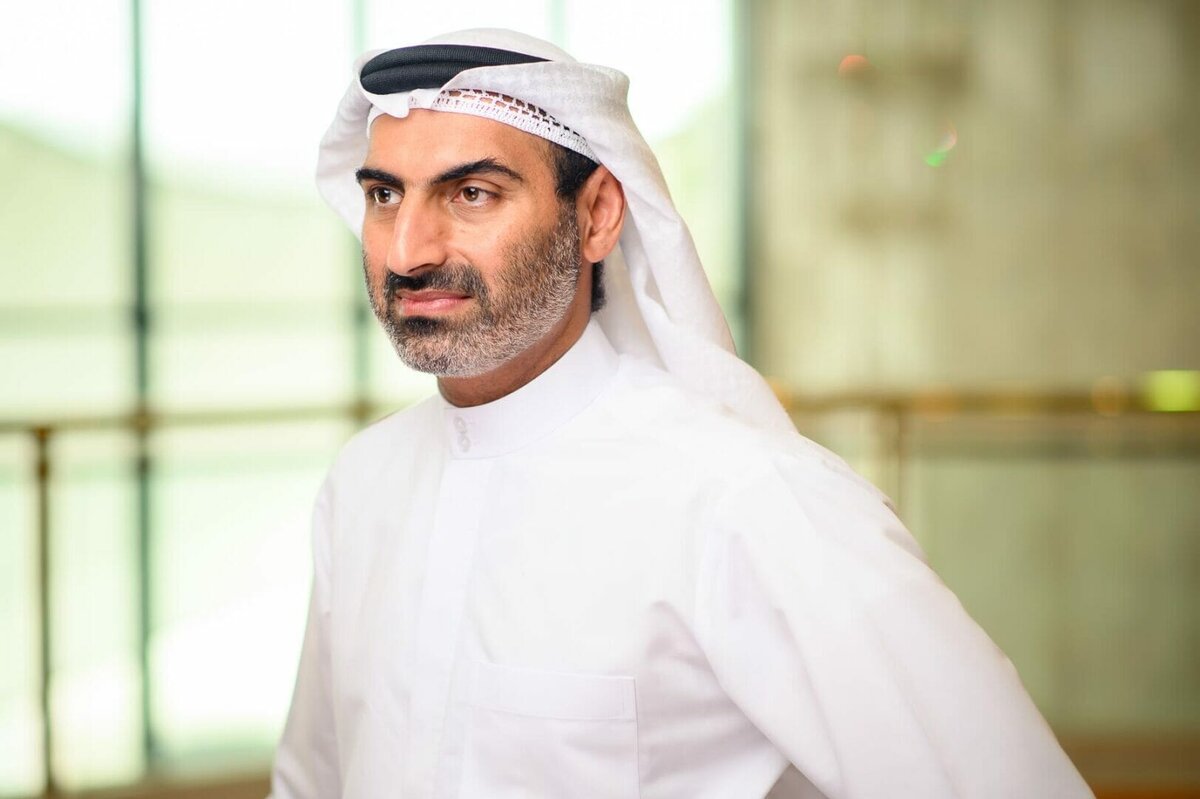
As the world looks to solve the ever-more complex energy trilemma, the energy efficiency of our built environment often remains a key – but overlooked – solution for addressing the needs of affordability, supply security, and emission reductions. Abdulrahman A Khansaheb, Managing Director of Khansaheb Industries, discusses the need to support the decarbonization and sustainability transition of the built environment, and the solutions available to us as we look to make our buildings ready for a zero-carbon future.
Embodied carbon is defined by the UK Green Building Council as the carbon emissions of a building created by its materials, including their extraction, transportation, construction, maintenance, replacement, and end of life treatment. These emissions have been found to contribute to 11% of global carbon emissions, and represent 28% of emissions originating from the built environment.
Optimising the whole life carbon of a building involves balancing overall reductions in embodied carbon and operational emissions. However, unlike operational emissions, embodied carbon impact is fixed at the time of, meaning that embodied carbon will account for around 50% of built environment emissions by 2035, as operational emissions of buildings reduce – but we carry on building.
Moreover, currently about 35% of buildings in the EU are 50 years old or older, and 97% of the building stock is not efficient enough to comply with future carbon reduction targets. These buildings will require deep, energy efficient renovation, even as operational emissions are reduced.
This suggests that, without action on embodied carbon, the UK’s 2050 net zero goal is not achievable. As a result, the Green Building Council has set out targets for all new buildings, infrastructure, and renovations to have at least 40% less embodied carbon by the year 2030.
There are a number of initiatives in development or delivery within the UK seeking to deliver this goal. For example, the proposed UK Green Taxonomy looks to set out a definition of a sustainable building, and the Greater London Authority’s 2021 London Plan requires development proposals to submit a circular economy statement explaining how materials will be disassembled, re-used, or recycled.
Environmental product declarations and material passporting, if implemented, are likely to also require building’s material composition and the environmental footprint of its products to be clearly outlined, in line with sustainable principles.
These activities suggest that embodied carbon is rising up the agenda whether regulators act or not. Life cycle assessments for public projects, alongside established certifications, such as BREEAM and LEED, also recognise the need to clearly outline a building’s environmental footprint. To achieve these targets, assessments will be needed to examine factors such as the type and volume of materials used within buildings and the carbon intensity of their manufacturing processes, the modes, and distances by which these materials are transported, and the processes by which these materials are maintained, removed, and finally treated at the end of life.

At Khansaheb Industries, we lead the production of Spiralite ductwork; a ventilation system made of cryogenic laminate non-metallic board, which looks to save energy and enable the development of structures fit for the low-carbon future, as we transition from heavily emitting building materials, such as steel.
Globally, steel is among one of the most important sources of material-related emissions within construction, with steel contributing around 7-9% of the global carbon emissions in 2018. Spiralite has been found to have contain 67% less embodied carbon in comparison to traditional steel ductwork, as well as maintaining air leakage rates at less than 1%, in turn bolstering energy efficiency, and helping to maintain low operational cost during times of spiralling energy bills.
Moreover, Spiralite’s transport emissions have been found to be 85% lower than its traditional steel counterpart, due to it being far lighter than metal ductwork and insulation, as well as arriving as a prefabricated kit to then be assembled onsite.
In summary, we must radically increase the pace and scope of the decarbonisation of our built environment, collaborating across the whole construction value chain to achieve the scale of change needed. The buildings sector will continue to grow to meet demand, but its growth must be in alignment with a zero-carbon future. To do so, decisionmakers in industry must embrace the transformation of their sector and invest in innovation, products and services which accelerate decarbonisation.