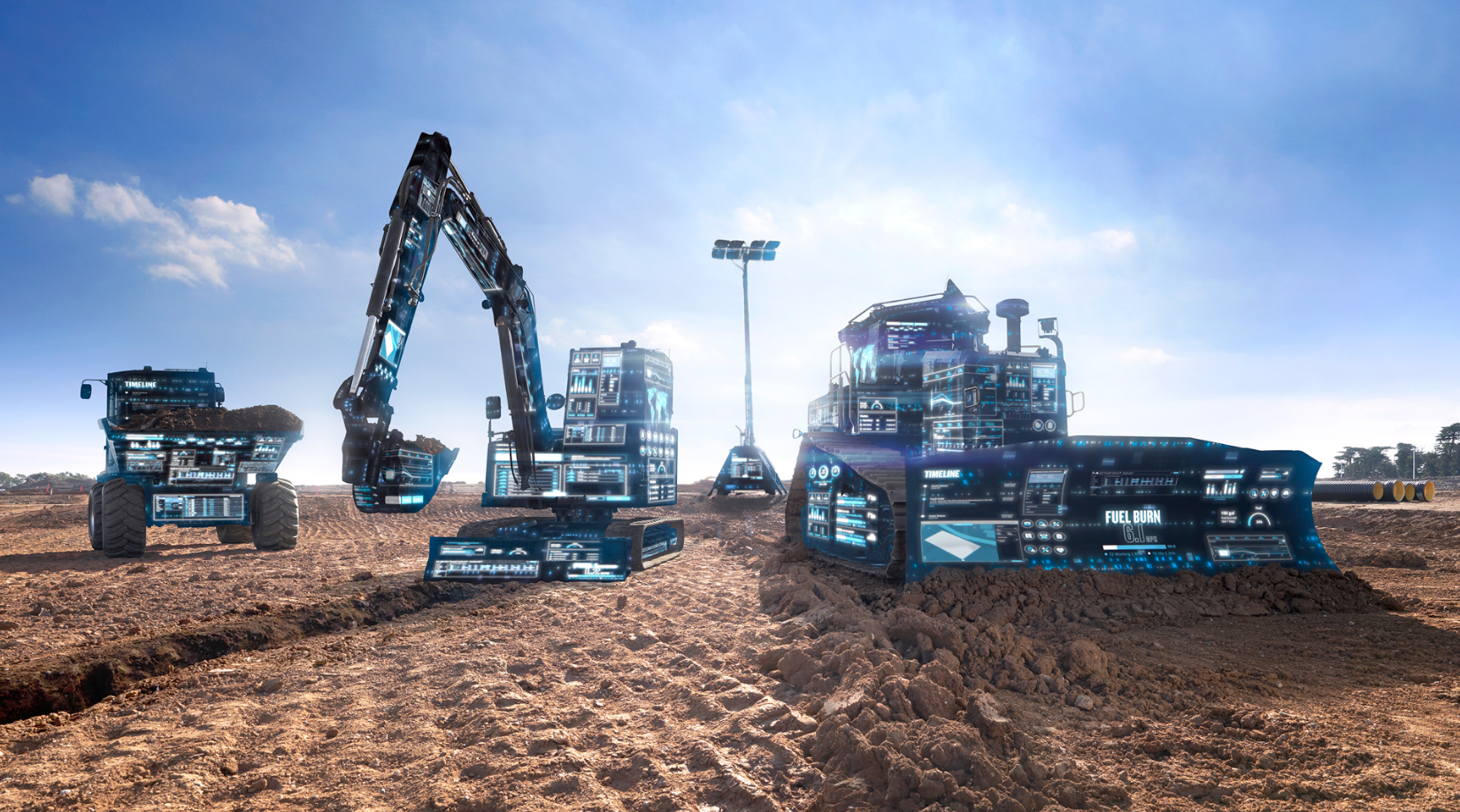
In response to demand for more user-friendly telematics technology on construction machinery, Finning has upgraded Cat® customers to a new software solution that delivers insights into fuel use and operational efficiency.
A new version of VisionLink is now available on all Cat machines to allow fleet managers to monitor machinery from one user-friendly web-based platform or smart phone app, which aims to maximise uptime, increase productivity and lower the cost of owning and operating equipment.
Trialled for a year on a ‘field follow’ system, Finning has worked alongside Cat to feedback on how fleet managers wanted the new technology to look and feel, with VisionLink now becoming a standalone Cat product.
Available for both new and existing machines, Finning is offering training to customers choosing the software to help them to get the most out of their machines and to fully understand how it can best serve their needs – whether that is for one machine or a large fleet.
Key changes to the technology include the ability to monitor all relevant elements of the machine’s operation package from one screen, to assign tasks to co-workers and to use a dynamic worklist to help manage the critical events surrounding fleets, in addition to still providing health data, utilisation, emissions and maintenance.
This supports economical use through lower fuel consumption, easier reporting on carbon footprint and a reduction in unplanned downtime through alerts and reminders.
The updated solution allows users to set targets that the performance of the machine can be evaluated against and reported on, such as runtime-specific data to display insights into operational use and idle time.
The software, when used with accompanying hardware, can be used to track the location of attachments to enable companies to know the location of valuable equipment as well as its machines. This is backed by geofence capabilities that will issue an alert if a machine is moved outside of a set boundary.
The new VisionLink technology will allow plant hire and construction companies to analyse fuel usage, operational hours, record hire status, location of assets and the operational hours of a machine.
Becky Wallis, Customer Support Supervisor for Technology at Finning, said: “Following customer feedback, a new Cat version of VisionLink was developed, which allows customers to see exactly what their stats are, how machines have been working, which products are being utilised. These insights allow the customers to get the most out of their machines with operational statistics helping to reduce issues such as idle costs or excess fuel burn.
“With more useability from a one-screen overview to text message alerts if machines are moved out of boundary, or if a fault is detected, the platform has been overhauled to make sure it offers exactly what customers want. It can even be used to request a service.
“The initial feedback has been great – the main driver behind the change was that site managers wanted to be able to see everything in one place, and the new platform does just that, whether you are sat at a laptop or assessing on the go from a mobile phone. The increased useability has been a great success to date.”
Reports can be delivered at daily or 10-minute intervals, to provide an overview of the day’s work, or an ongoing assessment of activity, while the new upgrade has added the choice to add notifications by text message to enhance accessibility when in use on site.
The software also allows QR codes to be used to bring up asset details, fault codes, information on when maintenance inspections are due and how full the fuel tank is.