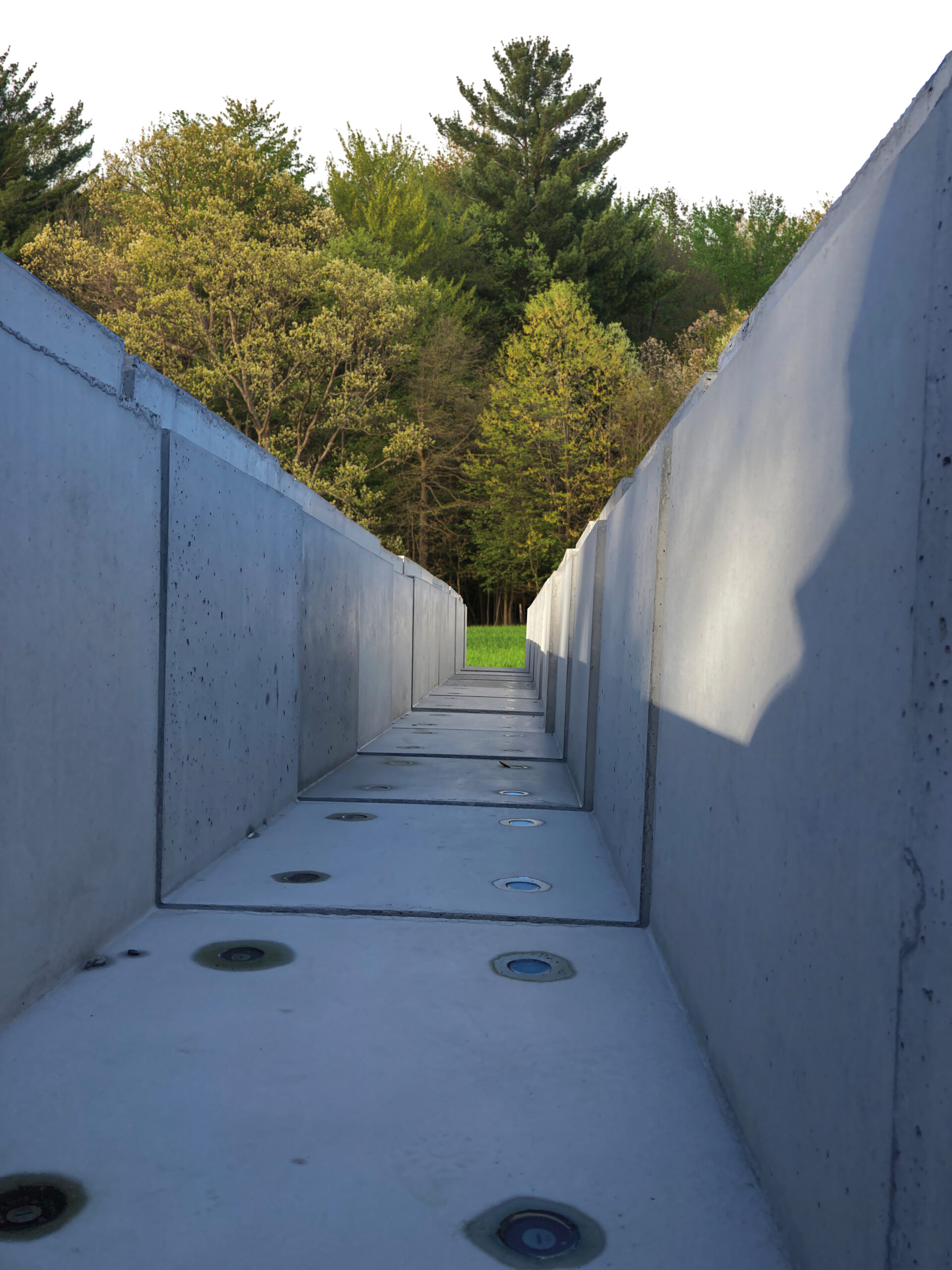
Ibstock precast concrete Utility Troughs and Lids provide total protection for large power and communication services as well as packing a significant environmental punch, delivering up to 60% less embodied carbon than traditional concrete mixes.
Ibstocks £60m investment in the new Atlas Ibstock brick factory in Walsall, is evidence of the Utility Troughs’ capabilities in action. Atlas has specified 66 linear metres of Ibstock’s concrete troughing to protect cabling across the factory floor.
Mark Hawes is Project Manager for the redevelopment of Atlas and has played a pivotal role in specifying products for the updated factory. He says: “As a key centre within Ibstock’s nationwide network of manufacturing facilities, the redevelopment of Atlas, as our most energy efficient clay brick factory, will play a critical role in accelerating the Ibstock Plc ambitions to reduce carbon by 40% by 2030 and achieve net zero by 2040.
“One of the key considerations for the Atlas project has been the materials we’re specifying within the factory. We want to ensure we’re installing products that are not only up to the rigours of a busy factory setting, but which are manufactured in a sustainable manner, wherever possible.
“It was that impetus which caused us to look within the Ibstock business and our own capabilities in manufacturing materials which feature significantly less embodied carbon than other market alternatives.
“The concrete troughs and lids range is a perfect example of that. Manufactured right here in the UK, the range includes straight, tee, cornered and angled troughs, meaning they can be easily adapted to the specific environments in which they’re specified.
“That flexibility was particularly important in the Atlas development, which had a number of tricky corners to consider. Thanks to the variety of angles found within the range, our contractors were able to install the product on bends or corners without compromising on the protection provided by the troughing.”
As an active brickmaking factory which has the capability to produce 105 million bricks per year, minimising downtime for any upgrade was absolutely imperative. That was another consideration which led to the specification of the troughs and lids.
Gary Armstrong was site manager for Hannafin Contractors Ltd worked on the Atlas project and was responsible for installing some of the 66 metres of troughing within the factory. He says: “From an installation point of view, the fact Ibstock’s troughs are manufactured in precast concrete means they arrived to site ready-to-install.
“Unlike concrete that is cast in-situ, we did not have to spend time installing the base or shuttering walls before installing the unit. This saved us a significant amount of time on site, and minimised the length of time in which the factory floor had to be shut down.
“The units are so easy to handle and install – even more complex angles, such as corners, are made simple by Ibstock’s solution, which comprised a blend of 1000 x 1000mm and 600 x 600mm service trenches.”
The Utility Troughs and lids can be found in a host of sectors, from manufacturing and communications to the rail sector. Alongside their robustness and user-friendliness, the systems are also fire resistant and tested to BS EN 1433 standards for the collection and conveyance of surface water.
To learn more about the complete range, please visit: https://www.ibstock.co.uk/products/rail-and-infrastructure/utility-troughs-and-lids
For more information, visit: https://www.ibstock.co.uk