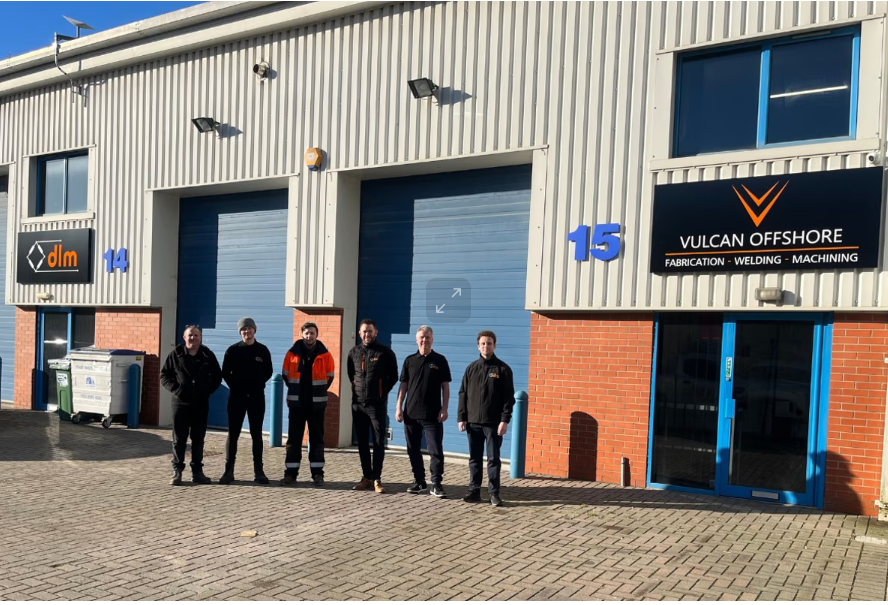
Dynamic Load Monitoring (UK) Ltd. (DLM), of Southampton, has opened a machine shop in collaboration with sister company, Vulcan Offshore Ltd.
Having taken a new lease on two buildings already fitted out as a machine shop in Vancouver Wharf, Southampton, each company will occupy an adjacent unit. A state-of-the-art suite of machining and milling equipment will give DLM full control of its manufacturing processes, reducing lead times.
DLM has supplied load cells plus load monitoring and cable working equipment to the lifting, rigging, wind energy and wider renewables sector for a decade. It often partners with Vulcan, which is a specialist in fabrication, welding, and computer numerical control (CNC) machining.
Demand has long since outstripped the capacity of Vulcan, which also performed subcontracted engineering, and DLM had no machining capability of its own. Previously, DLM would source the raw material—typically 17-4PH stainless steel—and outsource to a machinist that would machine the load cell billet according to drawings produced by the in-house design team. DLM would then complete strain gauging, assembly, proof load, calibration, and final tests.
Martin Halford, managing director at DLM, said: “This is most probably the largest single investment ever made by DLM and marks a real step forward for us in being able to control the complete manufacture of our products. It is something that we have wanted to do and have planned for a long time, but the opportunity came up when we least expected it to acquire this new premises. Vulcan has gone from strength to strength in its very short life. With the need for more space at our existing workshop [in Quayside Road] and the winning of some large contracts, the increased capacity and space will aid our growth even further and allow us to push on quicker with our plans.”
He added: “The CNC lathe [at Vulcan] was already at full capacity, even without DLM work; and we could rarely get access to it. Now we can free-up vital space in Vulcan’s workshop for another welding bay, which was desperately required due to the increase in order levels. We already source raw materials of the highest quality from approved mills in Western Europe; we will eventually stock popular sizes to further enhance efficiency and cut costs.”
Machining capability
The machine shop, which will feature two Doosan Puma lathes, a Haas lathe, and a Haas mill, will be supported by a dedicated team of five professionals, including a workshop manager jointly appointed by DLM and Vulcan. They will take orders from quotation, machining, gauging, documentation, shipment, and every stage in between. Traceability will thusly be enhanced.
The lathe is able to machine pins to 200mm diameter and over 1m in length, in capacities over 300t. However, Halford reiterated that the investment goes beyond machining load pins, the company’s flagship product, with tensile link billets and running line monitors (RLMs) also central to the newly expanded operation. The mill will machine the standard range of tensile links and both the company’s 60t and 200t capacity RLMs.
Halford said: “All our load pins are typically custom-designed to meet clients’ specific physical sizes, so although we state we have some standard [load pins] on our website, they are only standard in their electrical operation and sealing method / environmental protection—not necessarily their physical size or appearance. Our pins are used for various applications across numerous industries, including oil and gas, lifting, rigging, and subsea.”
DLM is renowned for supply of subsea load pins, especially, most commonly used in tandem with underwater trenching vehicles used to lay and bury cables. The pins measure the forces imparted on sections of the underwater vehicle and aid the control of the vehicle as well as monitoring its condition during operations.