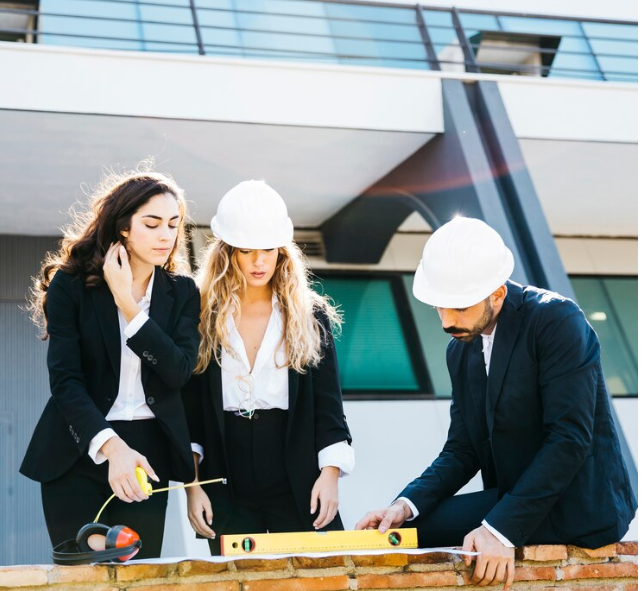
Modern construction businesses are faced with a distinctive set of challenges. You might find operations interrupted by poor weather, supply chain disruption, regulation, and labour shortages – to name but a few factors.
To improve the efficiency of your operation, and drive up the profitability of your business, it’s worth thinking proactively. What processes might you implement to improve things?
Enhance safety
Along with agriculture and offshore fishing, construction is among the deadliest industries. Commensurate with these risks is a sizeable volume of regulation designed to protect workers. The law requires, for example, that employers provide a safe working environment for employees. In construction, this might mean providing ongoing safety training, installing appropriate signage, and mandating the use of personal protective equipment like ear defenders, goggles, and hard hats.
Employee satisfaction
One of the major virtues of a robust health and safety policy is that it will drive down absenteeism, and drive up employee morale. Workers who feel safe, after all, will tend to be more productive.
But it’s worth addressing this directly. What can you do to make employees happier and more productive? You might support them through training, or the provision of the right tools and equipment. When employees feel that they are going to be able to progress within the company, they tend to enjoy better levels of morale.
HR software can help identify and address the needs of individual employees, which will help you to improve and retain these workers.
Streamline communications
One of the most obvious obstacles to effective work in the construction industry is miscommunication, which in some cases can lead to disputes. Make sure that you manage client expectations, and that you issue instructions to workers in a way that’s concise, clear, and easy to keep track of. Reporting apps can help you do this by keeping all communications related to a given project in the same place. That way, if there’s a problem, you’ll be able to look back and see when it was reported, and by whom.
Anticipate supply chain problems
Every construction project relies on a supply of materials and tools. In the modern world, business often limits warehousing costs by operating a ‘just in time’ policy when it comes to delivery. However, this imposes a risk: it means that, where delays occur, a project can be brought to a halt. This can cause costs to escalate, and customers to become unhappy.
Through planning, you can anticipate these problems, and implement measures to secure alternative solutions. For example, if you know that there are going to be strikes affecting public roads near you, you might arrange for essential shipments of cement, plaster, or bricks to be delivered ahead of time – or, you might consider other, more local suppliers