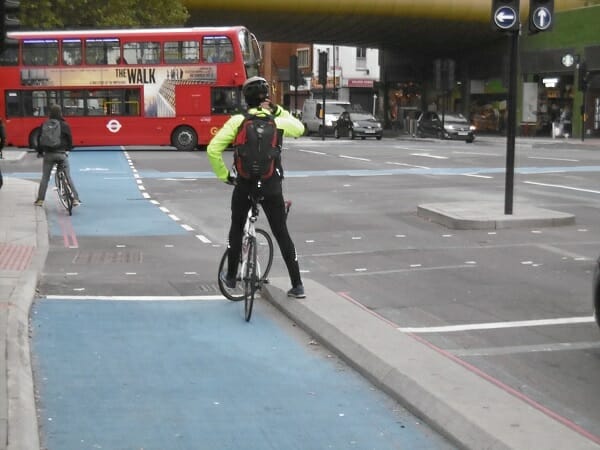
Charcon, the commercial hard landscaping division of Aggregate Industries, has manufactured and supplied 24,000l/m of Eco Countryside™ Cycle Kerb for the Mayor’s flagship Cycle Superhighway 2 (CS2) between Aldgate and Bow in London. The contract follows a major investment by Transport for London (TfL) to make the route safer for cyclists and other road users.
With more than 60 collisions involving injuries to cyclists recorded on the corridor annually, Charcon was commissioned by TfL in 2015 to design and deliver a solution that would literally save lives. In partnership with Ringway Jacobs, Charcon’s technical department designed an innovative 500mm-wide Eco Countryside Cycle Kerb segregation system as an alternative to granite kerb with a concrete block paving inlay previously used.
The bespoke design features a bull-nose edge running along the carriageway, capable of withstanding vehicular impact, while a full batter profile on the cycleway side significantly reduces the chance of cyclists catching a pedal. A frog in the base of the unit improves the key into the bedding material, further reducing the weight of the unit and assisting installation.
Being installed on both sides of the carriageway, the unique integrated system safely segregate cyclists from passing traffic, even when on the blind side of a lorry or bus.
Mike Davies, Specification and Major Projects Manager at Charcon, comments: “Cycle use in London has grown significantly since the introduction of the Cycle Superhighway network. CS2, running along the A11 between Aldgate and Bow roundabout, was one of the first implemented and is used by 2,000 cyclists in each direction daily. Cycle deaths on London roads average 16 per year, reaching 33 at its peak. Last year alone, eight cyclist deaths were reported. In light of this, TfL brought forward its improvements to the route, in line with updated London Cycling Design Standards.
“A key factor in the successful construction of the new cycleway was opting for the one unit concrete segregation system. This meant that much of the work could be done off site, thereby speeding up construction by around 50% and reducing impact on road users. Fewer materials were required on site, reducing the space needed for storage.
“Furthermore, the one unit system ensured that surfaces match both across and along the island. The result is a greater consistency of colour between the units than is usually achieved using natural granite with a block paving infill.”
In total, 24,000l/m of Eco Countryside Cycle Kerb were supplied for the CS2 project. The bespoke design offered a number of quantifiable benefits, including a cost saving of 25% and a 33% reduction in carbon footprint, versus natural granite imported from China. It also reduced the requirement for raw materials, and manufacturing units in the UK reduced the transportation carbon footprint and delivery times.
Installation time for construction of the island was reduced by 50%, which in turn impacted positively on the cost of preliminaries and traffic management. Overall, the development of the new unit has saved approximately £150K over the traditional approach. However, when it comes to quantifying the number of lives that will be safeguarded in the future thanks to the new segregation system, the cost saving is immeasurable.
To find out more, visit www.aggregate.com.