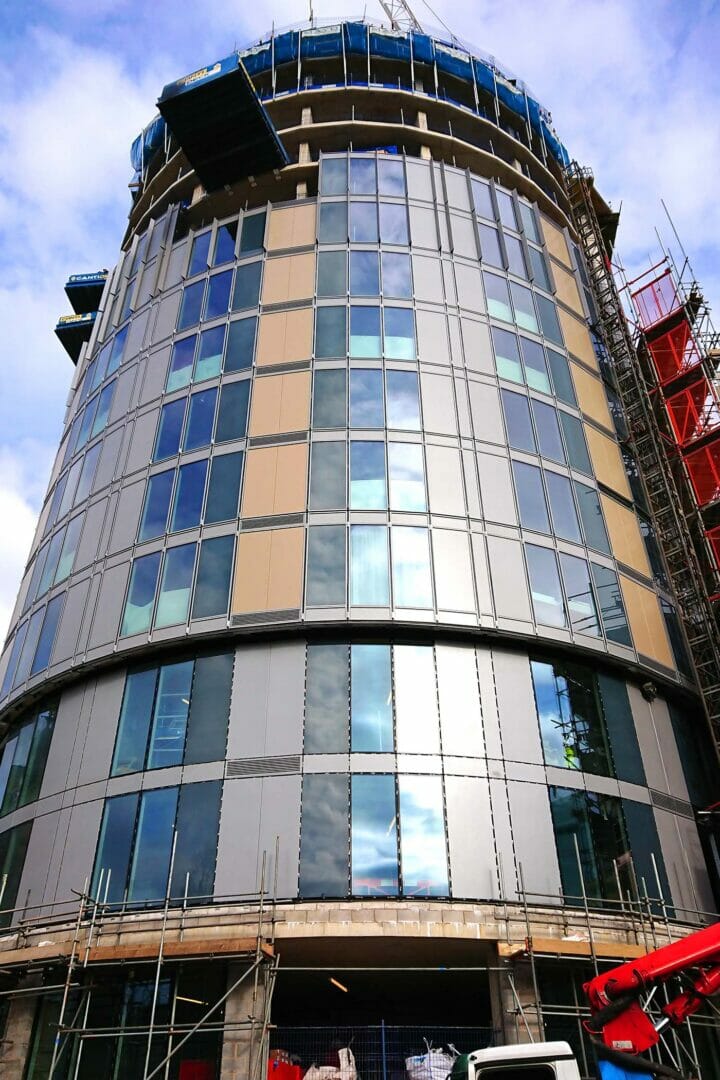
by Wojciech Brożyna – MD Aluprof UK
More specifiers in the UK are becoming aware that Unitised systems are becoming more affordable and available through UK fabrication specialists. Simple to install by experienced teams on site, unitised systems can speed up the completion of the building envelope on site, whilst also catering for greater building movement.
Tom Wells of Allford Hall Monaghan Morris Architects, comments, “Scotland Yard is the radical remodelling and extension of a 1930s building in Whitehall, to provide a new headquarters for the Metropolitan Police.
“The new west facade was designed as a more contemporary element using aluminium unitised curtain walling, manufactured in Poland by Aluprof. The system is a combination of glazed and solid bronze powder coated panels with a brise-soleil of different colour aluminium fins forming privacy and solar shading. The colour of the fins sampled the surrounding buildings, creating a rich tapestry which despite its modern form, complements its prestigious location.
“Aluprof were able to produce bespoke extrusions to suit the architectural design and engineered the system to meet the strict performance requirements, whilst also advising on delivery, logistics and erection. Due to tight access and proximity to neighbouring parliamentary buildings, the glazed and Louvre panels were craned to the roof, assembled together and then lowered into position in a matter of weeks.”
The choice of curtain wall construction for many years has been limited to the traditional ‘stick’ form of construction. Aluminium mullion and transom profiles prepared in the factory are assembled and fixed onto the building in a grid formation and later glazed on site with, or without, pressure plates. These systems offer an excellent solution for small or large areas of glazed facades.
A relatively simple concept, a unitised facade installation consists of individually glazed, aluminium framed, complete unitised elements being delivered and assembled on site. Each unit is complete and, once in place, seals effectively to its unitised neighbour and offers a complete weathered installation. The unitised solution often shortens the time required to complete the building envelope and can save weeks on a building programme.
Many of the very large facade companies in the UK and Europe specialise in unitised systems, but due to the nature of fabrication and logistics, will not consider projects under a certain value. These companies often hold the designs to the profiles and initiate weather testing on a ‘per project’ basis. For small to medium sized buildings in the UK we have therefore normally resorted to ‘stick’ curtain wall systems which are relatively easy to produce in a well equipped aluminium fabrication shop. Whilst these systems can be cost effective, they can take time to complete on site, often relying on wet sealing solutions in their construction so program progress can be slow in damp conditions, which is not ideal given the uncertainty of the British weather.
The most competitive stick systems comprise of 50mm mullion and transom sight lines which suit most construction requirement, but care is needed when calculating for allowable thermal and building movement. Unitised systems are complete facade elements which span from floor to floor and are often in standard module widths that allow for greater movement around their unitised perimeters than that of their stick system counterparts.
In today’s construction market, filling the supply gap between the huge facade contractors and the smaller to medium sized facade contractors are the aluminium ‘systems’ companies. These systems companies supply ‘off the shelf’ profiles complete with hardware solutions to the experienced fabricator and installation contractors. The systems are manufactured to strict guidelines, often laid down in a comprehensive technical manual, and once installed, perform to extensive weathering capabilities. Until a decade or so ago, no systems companies provided such unitised solutions.
Windows, doors and stick curtain wall systems can easily be produced on a typical fabrication line, as the completed products are of reasonable size which can be manually handled and easily delivered. Unitised construction requires a significant investment in new plant and machinery, as well as experience in manufacture, logistics and installation.
Manufacturing often requires a new production line with mechanical lifting equipment. Unitised systems are factory glazed and elements are typically up to 3.0m in height and 1.2m or more in width which weigh upward of 150kg once glazed. It is this fully glazed fabrication requirement for unitised construction which is not normally considered in a typical aluminium fabrication shop.
Logistics are also much different to normal commercial aluminium work. Whilst stick curtain wall systems, unglazed windows and doors can easily be packaged and loaded onto a flat bed lorry for transport, unitised modules are usually placed in racks which are either lifted off in their entirety on site, or when possible, unitised elements can be lifted off individually and installed direct from the delivery vehicle. As unitised elements take up little space and can be installed quickly, they are ideal for where site access is very tight and storage limited.
Where racks of complete elements are loaded to the floor where they are being installed, special plant is used for installation. These specialised machines pick up units from the rack, take them beyond the floor edge, turns the unit vertical and places it upon the fixing brackets, where the unit aligns with the edge seals of adjacent units.
Scaffolding is not required when the glazed facade is constructed of unitised elements. No applied ‘wet’ sealing is required on installation, so units can be installed in inclement weather, the only issue that does require monitoring is that of high winds. Being able to install without scaffolding and in damp weather ensures that the building envelope is watertight in the shortest space of time and importantly, to programme.
This leads us onto the third crucial element of unitised facade installation, that of setting out. A unitised element sits on two brackets fixed to the building structure, these brackets need to be set out accurately around the building on all floors prior to any units being delivered on site. Between the units there is a least two structural seals which link units together on all sides allowing for building and thermal movement whilst creating excellent weathertight and good thermal insulation properties.
As unitised systems are manufactured off site in a controlled environment, it is often claimed that such fabrication is conducted to a much higher standard. Due to the more specialist manufacture, logistics and installation, unitised systems are more expensive than traditional stick construction. Given that scaffolding is not required, the additional costs can be completely offset but with the added benefit of up to 50% reduction in time to install on site.
To ensure that the complete facade contract can be achieved with the correct expertise and appropriate efficiency, Aluprof offer UK support for their UK customers with start-up production assistance of unitised systems, offering both factory based and on site support, from experienced unitised engineers.
As one of Europe’s leading systems companies, Aluprof’s MB-SE75 competitively priced unitised curtain wall system has been extensively tested and used on many European and Worldwide projects. Projects in London are also under installation at this time. Our philosophy is one of bespoke design when in consultation with specifiers. Project details and solutions can be developed by our technical department in the UK before the project goes to tender to ensure that construction details are both robust and covered by Aluprof’s warranty.
Our Aluprof UK head office and extensive distribution centre is located in Altrincham, Cheshire. Our systems are increasingly being specified on a wide range of residential and commercial projects across the UK. Systems are designed, fabricated and installed by selected, specially trained companies, to ensure each fabricated product meets the Aluprof exacting standards. Further information is available on our company’s website at www.aluprof.eu and specialist advice is available directly from our UK offices on 0161 941 4005.