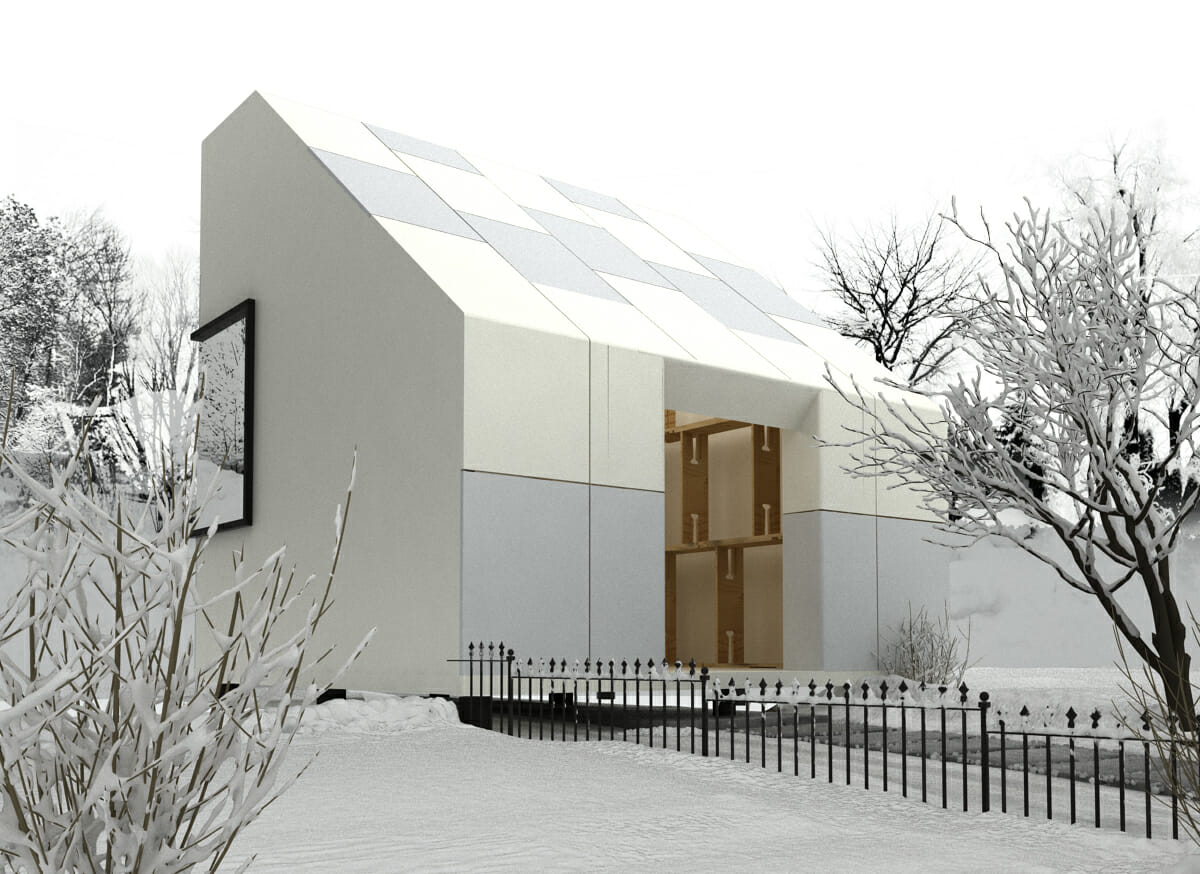
ClipHut is a parametrically generated structural system that is a direct response to Central European climate conditions and geography as well as regional building regulations. The idea for the system was developed by an interdisciplinary team at Ostwestfalen-Lippe University of Applied Sciences in Germany. A building designed using the ClipHut system could make use of any wood-based material, however, using material-efficient Kerto® LVL (laminated veneer lumber) products makes the building process fast, light and green.
The user inputs the desired building specifications within a grid of points into the ClipHut programming software and then specifies the geographic location and the intended use of the building. The ClipHut parametric model produces shop-drawings for a kit of parts in response to the particular needs of the user. The output is a structural grid configuration with components sized to meet local building code requirements.
The scale of the module, integrated numbering system and simple connections allow for easy assembly by even a layperson with limited construction experience. ClipHut buildings are also easily disassembled and reused. In an era when sustainability is one of the key requirements for construction, the ability to reuse the building parts significantly reduces waste and improves the environmental footprint of the building.
Innovative ideas shared openly
ClipHut received the Open Source Wood Award with the panel of experts praising its flexibility and innovative structural system that enables faster construction.
“We started out researching wood joints and in the end developed a building system. The system respects the properties of the wood material and optimizes its use”, explains the ClipHut team in their Open Source Wood submission.
The Open Source Wood Initiative by Metsä Wood is a collaborative online platform for architects and engineers to share their innovative ideas for modular wood construction. Users can upload their projects and concepts on the platform for feedback and collaboration opportunities. Metsä Wood’s experts evaluate the submissions and awards are given to the most innovative ideas, like ClipHut.
“ClipHut is the first idea I have seen where a handful of pieces could be used to construct almost any building shape. The use of plug-in connections between prefabricated components can offer fast installation on-site”, says Jussi Björman, Director of Technical Customer Service at Metsä Wood.
“We can see how sustainability is part of the Metsä Wood’s mindset,” says Thomaz Viera, the system developer of ClipHut. “If we want to develop construction industry in an increasingly environmentally conscious direction, we shouldn’t only invent better products. We also have to invest in a decentralized production and distribution chain, reducing our ecological footprint, increasing productivity and investing in mass customization solutions.”
Working with small-scale, lightweight Kerto LVL frames for a rigid structure
The loads acting on the structure are transferred through a series of small-scale framing layers, with each layer measuring approximately 1 metre. All of the components are precisely cut using a CNC milling machine to the specifications from the ClipHut parametric model. The original prototype was constructed from OSB (oriented strand board) to test the parameters of the system. The team sees Kerto LVL as a particularly suitable building material for ClipHut houses, because of its higher strength and superior strength-to-weight ratio, making the assembled structure extremely stable.
“Kerto LVL is of a high quality; it is tight and also stiffer than OSB and consequently the joints are able to hold more loads, allowing a bigger span between columns and reducing the need for material in some cases,” explains Viera. “Other advantages are the possibility to build higher or even add more floors to the building and also extend its life time.”
Bracing
Staggering vertical connections for improved stability
Vertical components are placed in each layer, providing lateral bracing that resist shear forces despite not having any diagonal components. Limiting the orientations to horizontal and vertical directions eliminated the need for complex angled connections and extra fasteners. Construction of the prototype showed that the components locked easily into each other and once each layer was complete, the structure as a whole was quite rigid as the frames worked together to provide lateral bracing.
Pre-milled clipping connections speed up construction
Horizontal plates are fabricated by a CNC milling machine with pre-cut slots that locate the vertical components, eliminating the need for any guessing or imprecise on-site measuring. Both ends of the vertical components are milled with the innovative clipping mechanism that slides into the horizontal components and locks securely into place. “It is a clip that can be bent inwards and connects and contracts the material through a milled pocket. This connection is completely milled into the material, which means it is prefabricated only to be constructed on site”, describes Jan Kahre Heidemann, professor and the project’s mentor at the University. The exact arrangement of all ClipHut elements is digitally documented and engraved on the connection during the CNC milling phase.
Flexible envelope options respond to local regulations
The behaviour of Kerto LVL in case of fire is well-known: the material is homogeneous and its charring rate is predictable. Design codes, especially in Europe, provide all the necessary information for safe design with LVL structures.
Responding to specific local fire regulations, a building based on the ClipHut system can be clad in non-combustible materials, allowing it to house a variety of uses from residential to commercial. The system is also flexible for different climates as a variety of wall assemblies can be easily carried out. Insulation, rain screens, heating systems and shading devices can all be incorporated in the ClipHut system. The facade is attached using small 3D printed clips that fasten to the structure with armatures, allowing for a continuous vented cavity outside of the structural grid.
An affordable and flexible constructing system using Kerto LVL
From the outset the ClipHut team had a clear vision: to develop new solutions in construction that make building more accessible and affordable. They achieve this by giving the ownership of design and documentation back to the user. “This means you don’t get the ready pieces delivered; instead you can then go with the file in hand to a carpenter or company, which can produce it. Otherwise, if you have access to certain machines, such as CNC or 3D printers, you can produce it yourself,” explains Maria Wilkens, the project manager of ClipHut. The innovative clipping connection allows for quick and easy construction and the use of Kerto LVL ensures an economy of materials and reduces the overall building costs. “Each material will bring advantages” explains Viera, “Kerto LVL, for sure, has all the properties needed to create a proper house and we are looking forward to building it!”