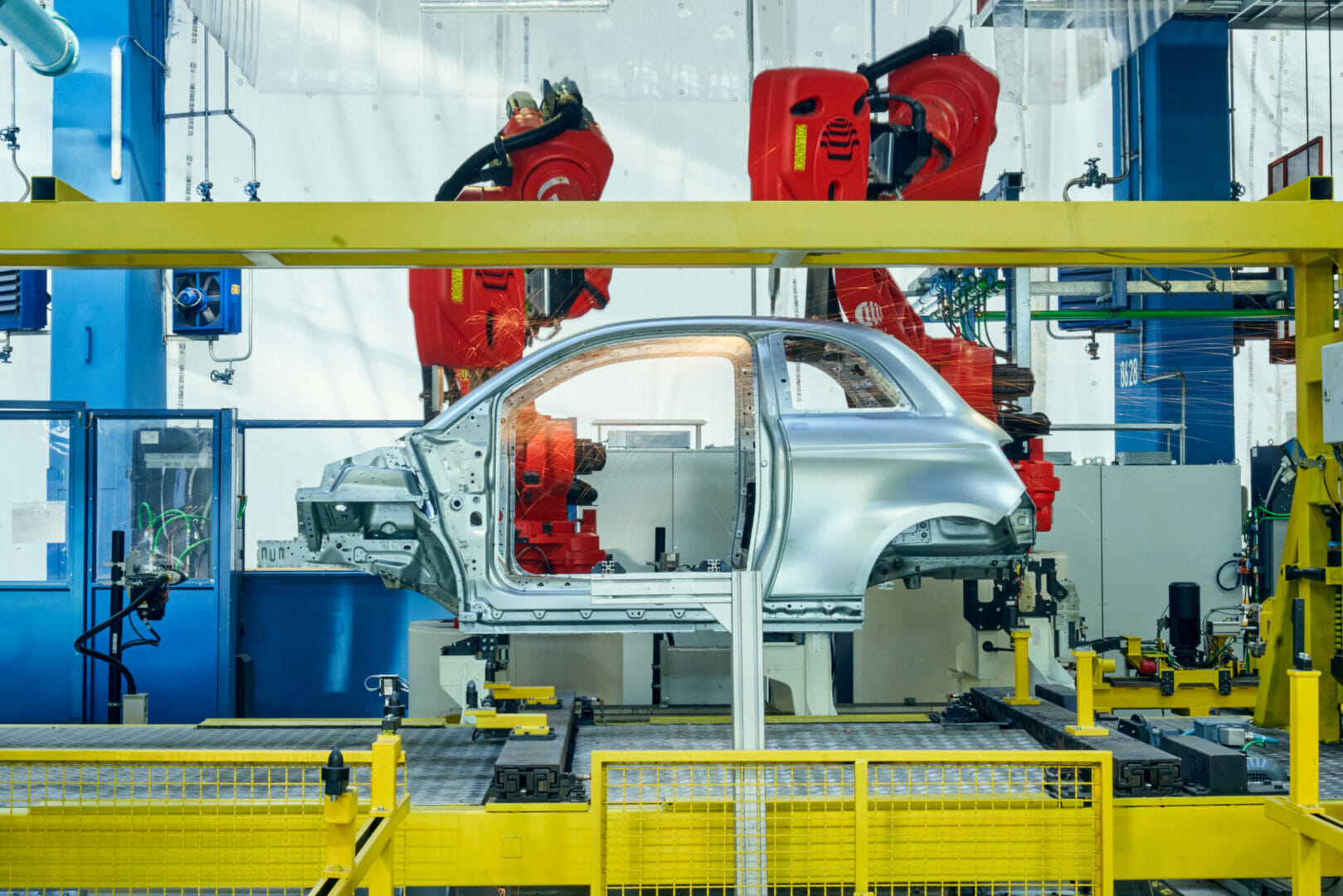
- The company has designed and deployed the manufacturing lines dedicated to the structural parts of FCA’s first fully electric vehicle, a Made in Turin product
- Comau worked alongside FCA and Fiat brand in reengineering the body to house the battery and transmission of the iconic vehicle
- A total of 187 next-generation Comau robots were used to build the New 500
- The robots were equipped with custom-designed handling systems for the electric vehicle including a special 3D-printed gripper
Grugliasco (Turin), November 26, 2020 – Comau is proud to have participated in the production of the New 500. The company has provided FCA and the Fiat brand with advanced automation solutions and its know-how in the development of innovative industrial processes to produce FCA’s first fully electric vehicle, a Made in Turin product.
The path started symbolically in July 2019 with the installation of the first Comau robot, which initiated the production line of the new full-electric model inside FCA’s historic Mirafiori plant. A total of 187 Comau robots were then integrated in the different phases of the car manufacturing process, thanks to the collaboration of a team of Comau experts who worked side-by-side the automaker’s designers to optimize the work lines in an excellent example of Smart Manufacturing. The team also needed to adapt the systems to a new body design of an iconic car while responding to the technical characteristics of a full-electric vehicle.
In particular, Comau has developed and equipped the body assembly lines dedicated to processing the structural parts of the New 500, including the front and rear floors, the bodysides and the framing, which are assembled and welded to give shape to the complete body of the car.
Each robot has been fully equipped by Comau to efficiently carry out all the special processes an electric car requires – from custom-designed handling systems and grippers to a special 3D printed end-effector for moving body components.
Comau has also integrated the lines with advanced vision systems to control the quality of the adhesive dispensing system, both during processing and at the end of the cycle. In order to optimize and speed-up inline tool changes, an articulated magazine system was designed to provide the robots with the different types of tools required to perform each application in a fast and easy way.
In addition, Comau has intervened in the design of the robotized line for the final assembly. After the bodyshop, which is used to form the body of the New 500, and the painting and surface treatment phases, all the internal parts are assembled and the single components of the car are optimized.
Andrew Lloyd, Chief Operating Officer – Electrification of Comau emphasized: “Our experience and global leadership in the industrial sector, together with the skills gained in the field of electrification and digitalization, support the creation of highly innovative, flexible and tailor-made technological solutions. This approach allows Comau to develop projects that look to the future of mobility and renewable energy sources, such as the New 500 full-electric, thus responding to the needs of an industrial system in continuous evolution and the demands of an end consumer increasingly attentive to sustainability”.
Comau
Comau, a member of the FCA Group, is a worldwide leader in delivering advanced industrial automation products and systems. Its portfolio includes technology and systems for electric, hybrid and traditional vehicle manufacturing, industrial robots, collaborative and wearable robotics, autonomous logistics, dedicated machining centers and interconnected digital services and products able to transmit, elaborate and analyze machine and process data. With over 45 years of experience and a strong presence within every major industrial country, Comau is helping manufacturers of all sizes in almost any industry experience higher quality, increased productivity, faster time-to-market and lower overall costs. The company’s offering also extends to project management and consultancy, as well as maintenance and training for a wide range of industrial segments. Headquartered in Turin, Italy, Comau has an international network of 7 innovation centers, 5 digital hubs, 8 manufacturing plants and employs more than 9,000 people in 14 countries. A global network of distributors and partners allows the company to respond quickly to the needs of customers, no matter where they are located throughout the world. Through the training activities organized by its Academy, Comau is also committed to developing the technical and managerial knowledge necessary for companies to face the challenges and opportunities of Industry 4.0.