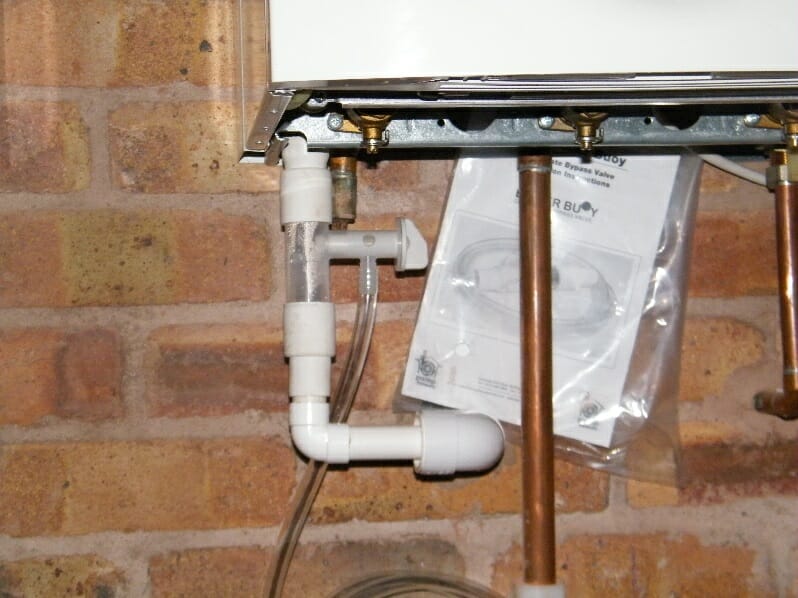
Paul Greengrass – Business Development Director at Pump House explains the challenges and solutions available for disposing and routing boiler condensate.
Amendments to the building regulations back in 2005 effectively made condensing boilers compulsory for both new build and boiler upgrades. The impact of this has led to condensate routing challenges and exposed pipework freezing.
Rules of thumb
Typically, a 24kW boiler will produce around 1.7 litres of condensate per hour, if running at full rate for the hour.
Depending on running hours, boiler output and system setup, annual volumes of 600 to 1200 litres of condensate can be produced.
The Big Freezing issue.
Many boilers include a siphon, which will dispose around 100ml of condensate at a time. This will help reduce any constant dripping which will exacerbate freezing. Typically, the siphon will activate 6,000 to 12,000 times per annum.
There is plenty of guidance in both the latest revision of BS 6798:2014 and the boiler manufacturer’s instructions, on the size of pipe and connection of condensate pipe to existing pipework.
The running and connection to external pipework were really defined as a last resort for use in exceptional circumstances, when internal connection is not viable. However, this exception has at times been the rule with some housing associations, experiencing 60% plus of condensate pipe being run externally.
The impact of such high levels of external pipe runs created serious problems during extended periods of sub-zero temperatures during winter months.
The optimum solution to avoiding freezing is to connect the condensate drain from the boiler to an existing internal sink, washing machine, bath, shower waste pipe or soil pipe.
If immediate access to the internal drain by gravity is not available, the fitting of a boiler condensate pump can offer advantages and flexibility of installation and keep the connection internal.
The Pump House 2 litre boiler condensate pump, which has a drink cycle of 750ml, will provide an 86% reduction in condensate cycles to around 800 per annum, when compared to a 100ml siphon.
Retro fitting options
When existing installations have external runs, which have the possibility of freezing, there are a number of options:
- Re direct the pipe work and route internally by gravity
- Re direct the pipe work and route internally using a condensate pump
- Fit a low-cost Boiler Buoy bypass valve on internal pipework
- Increase pipe size to at least 32mm and insulate with external grade PVC coated insulation
- Fit trace heating kit and insulate with external grade PVC coated insulation
Installation products and options
The resulting chaos caused by extended sub-zero temperatures with heating systems locking out, has resulted in a plethora of new options when external runs are the only practical option.
The cost of these solutions has been equally wide and varied: –
Boiler Buoy Bypass Valve – this is a very low-cost solution which incorporates a red ball to indicate when the pipe becomes blocked, and an internal bypass valve which can be switched to allow the boiler to keep working during the cold spell.
Insulation and Larger pipework – Increasing to 32mm and using a PVC coated insulation, can provide a reasonable level of mitigation and a moderate reduction in the risk of freezing. It is important to cover all external pipe, as any exposed pipe will be the weak link, especially bends and connectors.
Boiler Condensate Pump – the installation of a condensate pump can provide greater opportunity to connect the boiler condensate pipe to an existing internal waste pipe (sink, shower, bath or internal soil pipe) within the property, which can help reduce any risk of freezing pipework.
Our standard 2 litre condensate pump, when used in conjunction with external runs, will significantly reduce cycle times by pumping a large 750ml slug of condensate at 7 psi, further reducing the risk of freezing. The pump is typically only on for around 20 to 40 seconds at a time, with run annual times of only 3 to 4 hours and associated electrical consumption of around 200 to 300 watts per annum.
Trace heating – is a higher cost solution and has an electrical running cost impact to the house holder (4m length can be up to 25kW per annum), remember that trace heating still requires the pipe to be insulated (there is not point having an electric blanket in the winter without a duvet). The quality of the external stats on trace heating kit is important; the lower end products have low quality electronic components, the high-quality versions such as Frost Sentry have IP65 rated housings and robust electrical components.
Insulation advice and correct specification
The correct grade and thickness of insulation is also very important. The standard grey and silver coloured foam insulation, which is commonly available through most plumbing merchants, is for internal use only as it is not weather and waterproof. Soggy insulation will freeze around the pipe making freezing condensate worse.
One of the changes to BS 6798:2014 was to define the type of insulation to be used on external pipework, this should be a weather proof type with a PVC coating.
The use of the PVC coated weather and water proof type (19mm thick is recommended), importantly provides appropriate water vapour barrier, weather resistance and the PVC coating provides added strength and UV protection.
Pre-slit PVC coated insulation provides outstanding protection against freezing, for external boiler condensate pipework. This new design offers a quick and secure ‘tape free’ insulation, with its peel and seal joint, and its self-adhesive wrap over flap. Fully compliant with the Boiler Installation Standards BS6798:2014, the tough PVC coating is both weatherproof and UV stable.
This insulation is also ideal for use on air source heat pumps or biomass flow and return pipework, to avoid heat loss and meet the MIS 3005 requirements. To prevent cold bridging use it in conjunction with the Pump House TW-KIT a kit designed to insulate copper pipe, this ensures the pipework is fully insulated from the exterior to the interior of the property.
See our You Tube video demonstration on: https://youtu.be/63UoH8wq2-Y
Alternative options are to use external grade plastic trunking, which not only protects the insulation but provides a professional looking finish.
Soak Away imperatives
The use of a soak away not only provides a drain outlet, but more importantly provides neutralisation. BS 6798 calls for a 400mm deep hole, 300mm diameter, with a preformed plastic drain pot. If installed correctly the soak away should include around 25kg of lime chippings, to provide both adequate drainage and neutralisation.
A Geotextile membrane liner is also recommended to prevent soil and root ingress into the soak away.
The pipework to a soak away should be treated in the same way as other external pipe and insulated with the correct external grade and UV stable insulation.
For more information on installation guidance, or for a list of Stockist, please contact Pump House sales on +44(0)115 900 5858 or e-mail: sales@pumph.co.uk